Abrasive wheel end face and cylindrical finishing method
A grinding wheel and end face technology, which is applied in the field of grinding wheel end face and outer circle dressing, can solve the problems of affecting accuracy and service life, low grinding quality of parts, and unguaranteed dressing quality, etc., and achieves fewer intermediate links, improved grinding accuracy, and reliability sex high effect
- Summary
- Abstract
- Description
- Claims
- Application Information
AI Technical Summary
Problems solved by technology
Method used
Image
Examples
Embodiment Construction
[0012] Such as figure 1 , 2 As shown: the present invention mainly uses the diamond pen 9 for outer circle dressing, the diamond pen 10 for end face dressing, the end face and outer circle grinding wheel dresser 8, the reciprocating carriage 11 for realizing the precise dressing of the end face of the grinding wheel and the feed drag for realizing the precise dressing of the outer circle of the grinding wheel Board 6 is implemented. The method of the present invention is to adopt the mode of step-by-step linkage trimming of the end face and the outer circle, fix the grinding wheel 12 to be trimmed on the reciprocating carriage 11 through the grinding head device, start the grinding head device and drive the grinding wheel 12 to rotate, and the diamond pen 9 and 10 is installed on the dresser 8, and the dresser 8 is fixed on the feed carriage 6 of the machine tool. The radial position change of the grinding wheel 12 is realized by the feed stepper motor 7 driving the feed carr...
PUM
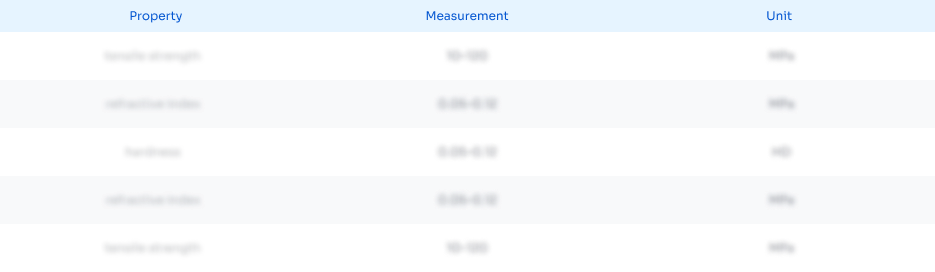
Abstract
Description
Claims
Application Information

- R&D
- Intellectual Property
- Life Sciences
- Materials
- Tech Scout
- Unparalleled Data Quality
- Higher Quality Content
- 60% Fewer Hallucinations
Browse by: Latest US Patents, China's latest patents, Technical Efficacy Thesaurus, Application Domain, Technology Topic, Popular Technical Reports.
© 2025 PatSnap. All rights reserved.Legal|Privacy policy|Modern Slavery Act Transparency Statement|Sitemap|About US| Contact US: help@patsnap.com