Production method of large-sized duplex metal composite board and device thereof
A manufacturing device and bimetallic technology, which is applied in the field of manufacturing large-scale bimetallic composite plates, can solve the problems of the difficulty in accurately controlling the interface layer by the double crystallizer compounding method, difficulty in manufacturing large-scale composite plates, and few production applications.
- Summary
- Abstract
- Description
- Claims
- Application Information
AI Technical Summary
Problems solved by technology
Method used
Image
Examples
Embodiment Construction
[0018] Figure 1, figure 2 , shown in Fig. 3, the manufacturing device of large-scale bimetallic composite panel of the present invention, comprises machine base 1, induction heater 2, slit type insulation pouring device 3, retaining structure 4, conveying mechanism 5, vibrating mechanism 6 and insulation agent cover device7.
[0019] The base 1 includes a frame 11 and a sealed chamber 12 mounted on the frame 11 with sealing properties.
[0020] The airtight chamber 12 is made of heat-resistant glass or steel plate, and its size can ensure that the induction heater 2, the slot-type heat preservation pourer 3 and the heat preservation agent cover 7 are included, so that the preheated substrate 8 is melted in the casting cladding metal. Body and thermal insulation agent are not in contact with air before, when the protective gas is passed in the sealed chamber 12, an oxygen-free and atmosphere-protected environment is formed, which prevents the steel plate from being oxidized du...
PUM
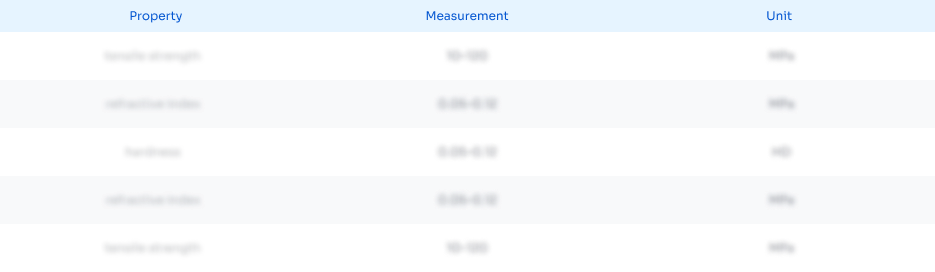
Abstract
Description
Claims
Application Information

- R&D
- Intellectual Property
- Life Sciences
- Materials
- Tech Scout
- Unparalleled Data Quality
- Higher Quality Content
- 60% Fewer Hallucinations
Browse by: Latest US Patents, China's latest patents, Technical Efficacy Thesaurus, Application Domain, Technology Topic, Popular Technical Reports.
© 2025 PatSnap. All rights reserved.Legal|Privacy policy|Modern Slavery Act Transparency Statement|Sitemap|About US| Contact US: help@patsnap.com