Space sailboard bending and turning mode vibration simulation active control device and method
A technology of torsional mode and bending mode, applied in the active control device and field of space sailboard bending and torsional mode vibration simulation, which can solve false suppression, optimization of the number and position of piezoelectric ceramic sheets, large flexible sailboard structure Rapid vibration control does not solve problems such as well, to achieve the effect of increasing driving capacity and overcoming stability problems
- Summary
- Abstract
- Description
- Claims
- Application Information
AI Technical Summary
Problems solved by technology
Method used
Image
Examples
Embodiment Construction
[0043] The present invention will be further described below with reference to the drawings and embodiments, but the scope of protection claimed by the present invention is not limited to the scope expressed by the embodiments.
[0044] The active control device for bending and torsional modal vibration simulation of flexible space sailboard is figure 1 The test device shown, such as figure 1 As shown, an epoxy resin board with an extension size of 1045mm×500mm×1.78mm (length, width, and height, respectively, x, y, and z in the coordinate system) of the flexible board 3 is selected as the simulated flexible space sail Board, the modulus of elasticity of epoxy resin board is E p =34.64GPa, the density is ρ p =1865kg / m 3 . The mechanical support clamping device 14 includes a flat rectangular base plate, a rectangular columnar support and an isosceles trapezoidal splint. The splint is used to clamp the flexible board 3. The clamping end of the flexible board 3 is processed, and bol...
PUM
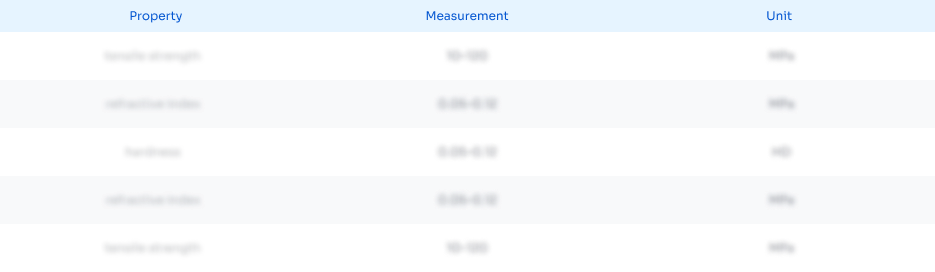
Abstract
Description
Claims
Application Information

- R&D
- Intellectual Property
- Life Sciences
- Materials
- Tech Scout
- Unparalleled Data Quality
- Higher Quality Content
- 60% Fewer Hallucinations
Browse by: Latest US Patents, China's latest patents, Technical Efficacy Thesaurus, Application Domain, Technology Topic, Popular Technical Reports.
© 2025 PatSnap. All rights reserved.Legal|Privacy policy|Modern Slavery Act Transparency Statement|Sitemap|About US| Contact US: help@patsnap.com