Measurement method of electro discharge machining gapping place
A technology of electrical discharge machining and measurement method, applied in mechanical gap measurement, metal processing equipment, measuring/indicating equipment, etc., can solve the problems of good insulation, not reflecting the processing gap, poor insulation, etc., to achieve low cost, no principle Error, the effect of simple and easy operation
- Summary
- Abstract
- Description
- Claims
- Application Information
AI Technical Summary
Problems solved by technology
Method used
Image
Examples
Embodiment Construction
[0014] The embodiments of the present invention are described in detail below in conjunction with the accompanying drawings: this embodiment is implemented on the premise of the technical solution of the present invention, and detailed implementation methods and specific operating procedures are provided, but the protection scope of the present invention is not limited to the following the described embodiment.
[0015] 1. The electrode is made of 10×10mm tetragonal graphite electrode ED-4 (Japan Ibidan Co., Ltd.), and the upper and lower sides of the workpiece (material: carbon tool steel SK3, size 30×30×15) are ground on the grinding machine . And use sandpaper to grind the end face of the electrode and the surface of the workpiece to bright.
[0016] 2. Install the workpiece on the worktable of the NC electric discharge machine (MARK X) produced by Sodick Co., Ltd. in Japan, so that the plane of the workpiece is parallel to the coordinate XOY and clamped. The electrode is...
PUM
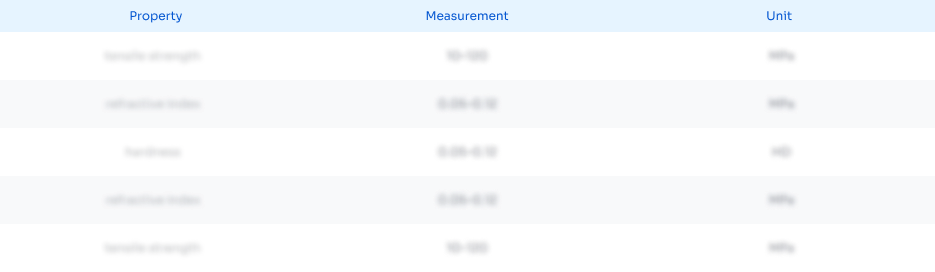
Abstract
Description
Claims
Application Information

- Generate Ideas
- Intellectual Property
- Life Sciences
- Materials
- Tech Scout
- Unparalleled Data Quality
- Higher Quality Content
- 60% Fewer Hallucinations
Browse by: Latest US Patents, China's latest patents, Technical Efficacy Thesaurus, Application Domain, Technology Topic, Popular Technical Reports.
© 2025 PatSnap. All rights reserved.Legal|Privacy policy|Modern Slavery Act Transparency Statement|Sitemap|About US| Contact US: help@patsnap.com