Method of welding thermistance chip and down lead
A thermistor and welding method technology, applied in resistors, welding equipment, non-adjustable metal resistors, etc., can solve the problems of voltage resistance drop, short preheating time, large welding temperature difference, etc., and achieve a small reduction in voltage resistance. , the effect of improving lasting reliability and reducing the probability of failure
- Summary
- Abstract
- Description
- Claims
- Application Information
AI Technical Summary
Problems solved by technology
Method used
Image
Examples
Embodiment Construction
[0022] The invention provides a method for welding a chip and a lead wire of a thermistor, which is used in the thermal resistance manufacturing process to weld the chip and the lead wire manufactured in the previous steps into one, and it includes the following steps:
[0023] In the preparation step, the lead wires are formed on the wire bonding machine according to the required line shape, and then the electrode-plated chips are inserted into the wire row according to the standard to be welded, and the step-type hot air welding machine is started, as shown in Figure 2, the welding machine furnace There are low-temperature preheating zone, high-temperature preheating zone, welding zone and heat preservation zone in sequence from the entrance to the exit. As shown in Figure 3, the temperatures of the low-temperature preheating zone, high-temperature preheating zone and welding zone are respectively set 80±10°C, 180±10°C, 270±50°C, and the temperature of the heat preservation a...
PUM
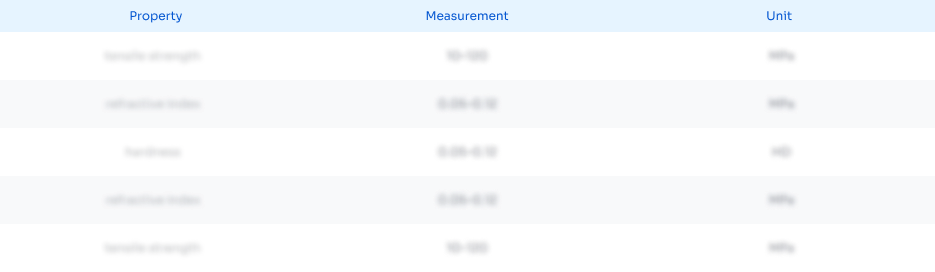
Abstract
Description
Claims
Application Information

- R&D Engineer
- R&D Manager
- IP Professional
- Industry Leading Data Capabilities
- Powerful AI technology
- Patent DNA Extraction
Browse by: Latest US Patents, China's latest patents, Technical Efficacy Thesaurus, Application Domain, Technology Topic, Popular Technical Reports.
© 2024 PatSnap. All rights reserved.Legal|Privacy policy|Modern Slavery Act Transparency Statement|Sitemap|About US| Contact US: help@patsnap.com