Processing technology for molybdenum and tungsten oxidized ore
A technology of tungsten oxide ore and oxide ore, which is applied in flotation, chemical instruments and methods, solid separation, etc., can solve the problems of high recovery cost of molybdenum-tungsten oxide ore and low technical and economic indicators
- Summary
- Abstract
- Description
- Claims
- Application Information
AI Technical Summary
Problems solved by technology
Method used
Image
Examples
Embodiment 1
[0033] The object of the present invention can be achieved through the following measures:
[0034] Processing method of the present invention is as follows:
[0035] A. The raw material is molybdenum tungsten oxide ore, crushed to -200 mesh, accounting for 43%, and the dissociation degree of mineral monomers is ≥70%;
[0036] B. Using water glass, kerosene, 2 # Oil or sodium hexametaphosphate, copper sulfate, butyl xanthate flotation molybdenum sulfide in molybdenum tungsten oxidized ore, and the rough concentrate is refined to obtain molybdenum sulfide concentrate;
[0037] C. Classify the flotation tailings of sulfide ore, the classification particle size is 30 μm, the coarse-grained grade enters the coarse sand roughing process, and the fine-grained grade enters the slime roughing process;
[0038] D. The mud sand system uses sodium carbonate or sodium hydroxide or lime as the slurry regulator, and the dosage range is 300 g / ton ore; sodium silicate is the gangue inhibito...
Embodiment 2
[0043] The object of the present invention can be achieved through the following measures:
[0044] Processing method of the present invention is as follows:
[0045] A. The raw material is molybdenum tungsten oxide ore, crushed to -200 mesh, accounting for 49%, and the dissociation degree of mineral monomers is ≥70%;
[0046] B. Using water glass, kerosene, 2 # Oil or sodium hexametaphosphate, copper sulfate, butyl xanthate flotation molybdenum sulfide in molybdenum tungsten oxidized ore, and the rough concentrate is refined to obtain molybdenum sulfide concentrate;
[0047] C. Classify the flotation tailings of sulfide ore, the classification particle size is 80μm, the coarse-grained grade enters the coarse sand roughing process, and the fine-grained grade enters the slime roughing process;
[0048] D. The mud sand system uses sodium carbonate or sodium hydroxide or lime as the slurry regulator, and the dosage range is 400 g / ton ore; water glass is the gangue inhibitor, an...
Embodiment 3
[0053] The object of the present invention can be achieved through the following measures:
[0054] Processing method of the present invention is as follows:
[0055] A. The raw material is molybdenum tungsten oxide ore, crushed to -200 mesh, accounting for 53%, and the dissociation degree of mineral monomers is ≥70%;
[0056] B. Using water glass, kerosene, 2 # Oil or sodium hexametaphosphate, copper sulfate, butyl xanthate flotation molybdenum sulfide in molybdenum tungsten oxide ore, and the rough concentrate is selected to obtain molybdenum sulfide concentrate;
[0057] C. Classify the flotation tailings of sulfide ore, the classification particle size is 150μm, the coarse-grained grade enters the coarse sand roughing process, and the fine-grained grade enters the slime roughing process;
[0058] D. The mud sand system uses sodium carbonate or sodium hydroxide or lime as the slurry regulator, and the dosage range is 1000 g / ton of ore; sodium silicate is the gangue inhibi...
PUM
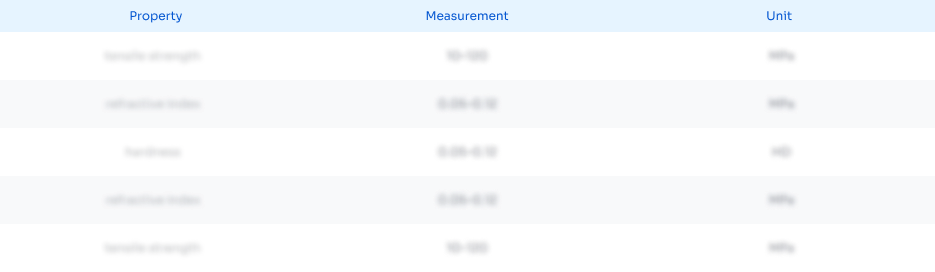
Abstract
Description
Claims
Application Information

- R&D
- Intellectual Property
- Life Sciences
- Materials
- Tech Scout
- Unparalleled Data Quality
- Higher Quality Content
- 60% Fewer Hallucinations
Browse by: Latest US Patents, China's latest patents, Technical Efficacy Thesaurus, Application Domain, Technology Topic, Popular Technical Reports.
© 2025 PatSnap. All rights reserved.Legal|Privacy policy|Modern Slavery Act Transparency Statement|Sitemap|About US| Contact US: help@patsnap.com