Micro-alloying refined synthetic slag and preparation method thereof
A technology of refining synthetic slag and microalloying, which is applied in the field of iron and steel smelting and manufacturing, and can solve the problems of increasing production costs, increasing labor intensity of workers, and low grade of niobium ore
- Summary
- Abstract
- Description
- Claims
- Application Information
AI Technical Summary
Problems solved by technology
Method used
Examples
preparation example Construction
[0016] The preparation method of microalloying refining synthetic slag, the steps are as follows:
[0017] Break vanadium-containing waste, lime, fluorite and silicon carbide into powders with a particle size of less than 0.5mm, mix them in proportion, melt them at 600-800°C, add nitrogen-enhancing agents during the pre-melting process, release the slag and cool it to room temperature, that is Microalloying refining synthetic slag is obtained.
[0018] Further preferably, the micro-alloying refining synthetic slag obtained in the above steps is added with an appropriate amount of binder to form a φ10-20mm spherical synthetic slag and dried at a low temperature of 30-50°C.
[0019] The binder is a conventional binder for pelletizing synthetic slag, which can be water glass, asphalt, or phosphate. The amount of the binder is not particularly limited in the present invention, and it can be used according to the prior art in the field. For example, the amount of the binder can be...
Embodiment 1
[0026] Micro-alloying refining synthetic slag, raw material composition weight parts are: 20 parts of vanadium-containing waste material, 60 parts of lime, 2 parts of fluorite, 10 parts of silicon carbide, and 8 parts of nitrogen-enhancing agent silicon nitride balls.
[0027] Preparation:
[0028]Break the vanadium-containing waste, lime, fluorite and silicon carbide into powders with a particle size of less than 0.5mm, mix them in proportion, melt them at 700°C, add nitrogen additives during the pre-melting process, release the slag and cool it to room temperature, and then refill 8% of the total mass of synthetic slag is binder water glass, resulting in φ10-20mm spherical synthetic slag, which is then dried at a low temperature of 40°C, and the moisture content of the product should be lower than 5%wt.
Embodiment 2
[0030] Micro-alloying refining synthetic slag, raw material composition weight parts are: 15 parts of vanadium-containing waste material, 65 parts of lime, 1.5 parts of fluorite, 10 parts of silicon carbide, 6 parts of silicon nitride ball of nitrogen increasing agent.
[0031] Preparation:
[0032] Break the vanadium-containing waste, lime, fluorite and silicon carbide into powders with a particle size of less than 0.5mm, mix them in proportion, melt them at 750°C, add nitrogen additives during the pre-melting process, release the slag and cool it to room temperature, and then refill 6% of the total mass of the synthetic slag is binder water glass to form a φ10-20mm spherical synthetic slag and dry it at a low temperature of 50°C. Product moisture should be less than 5%wt.
PUM
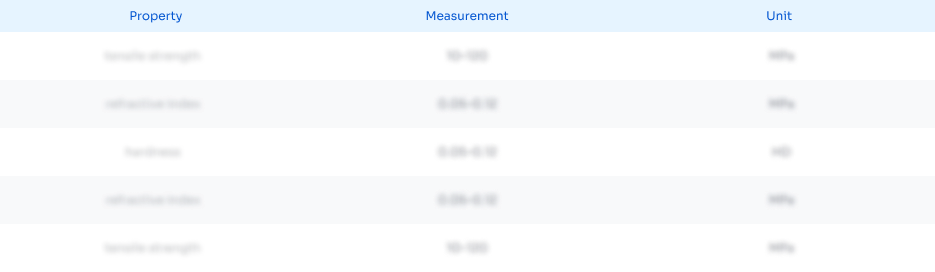
Abstract
Description
Claims
Application Information

- R&D
- Intellectual Property
- Life Sciences
- Materials
- Tech Scout
- Unparalleled Data Quality
- Higher Quality Content
- 60% Fewer Hallucinations
Browse by: Latest US Patents, China's latest patents, Technical Efficacy Thesaurus, Application Domain, Technology Topic, Popular Technical Reports.
© 2025 PatSnap. All rights reserved.Legal|Privacy policy|Modern Slavery Act Transparency Statement|Sitemap|About US| Contact US: help@patsnap.com