Combined preparation method for ethylene diamine and aminoethylpiperazine
An amine ethyl piperazine and a combined preparation technology are applied in the field of joint preparation of ethylenediamine and amine ethyl piperazine, can solve the problem of low yield of ethyl piperazine and the like, and achieve the effect of improving the yield
- Summary
- Abstract
- Description
- Claims
- Application Information
AI Technical Summary
Problems solved by technology
Method used
Image
Examples
Embodiment 1
[0023] 1.1 Preparation of catalyst
[0024] a. Phosphorus-modified mordenite catalyst
[0025] Take 80g of mordenite, add 20g of alumina and 5mL of water, granulate, shape, press into Φ5×5mm cylindrical particles, dry and roast at 500°C for 2 hours to obtain a catalyst precursor;
[0026] 50 g of the catalyst precursor was added to a solution prepared by 54 mL of n-hexane and 3.4 g of trimethyl phosphate for impregnation, and the n-hexane was distilled off at 90°C. The residue after evaporating to dryness was heated up to 550° C. in a muffle furnace at 3° C. / min, calcined for 5 hours, and cooled naturally to obtain a 1.5% phosphorus-modified mordenite catalyst.
[0027] b. Silicon modified ZSM-5 zeolite catalyst
[0028] Take 80g of ZSM-5 zeolite, add 20g of alumina and 5mL of water, granulate, shape, press into Φ5×5mm cylindrical particles, dry and roast at 500°C for 2 hours to obtain the catalyst precursor;
[0029] 50 g of catalyst precursor was added to a solution prepa...
Embodiment 2
[0035] 2.1 Preparation of catalyst
[0036] a. Phosphorus-modified mordenite catalyst
[0037] The catalyst preparation process is basically the same as in Example 1, except that the solution prepared by 58 mL of n-hexane and 4.7 g of trimethyl phosphate is used for impregnation to obtain a 2.1% phosphorus-modified mordenite catalyst.
[0038] b. Silicon modified ZSM-5 zeolite catalyst:
[0039] The catalyst preparation process is basically the same as in Example 1, except that the solution prepared by 50 mL of n-hexane and 17.5 g of phenyltrimethoxysilane is used for impregnation to obtain a 5.0% silicon-modified ZSM-5 zeolite catalyst.
[0040] 2.2 Amination reaction
[0041] Mix ethanolamine and ammonia, preheat and vaporize, pass into a fixed-bed reactor, and react in the presence of a condensation amination catalyst of 2.1% phosphorus-modified mordenite catalyst, the pressure is 5.0MPa, the temperature is 300°C, the weight of ammonia and ethanolamine The ratio is 6:1, ...
Embodiment 3
[0045] 3.1 Preparation of catalyst
[0046] a. Phosphorus-modified mordenite catalyst
[0047] The catalyst preparation process is basically the same as in Example 1, except that the solution prepared by 70 mL of n-hexane and 4.1 g of trimethyl phosphate is used for impregnation to obtain a 1.8% phosphorus-modified mordenite catalyst.
[0048] b. Silicon modified ZSM-5 zeolite catalyst
[0049] The catalyst preparation process is basically the same as in Example 1, except that the solution prepared by 50 mL of n-hexane and 8.8 g of phenyltrimethoxysilane is used for impregnation to obtain a 2.5% silicon-modified ZSM-5 zeolite catalyst.
[0050] 3.2 Amination reaction
[0051] Mix ethanolamine and ammonia, preheat and vaporize, pass into a fixed-bed reactor, and react in the presence of a condensation amination catalyst of 1.8% phosphorus-modified mordenite, with a pressure of 2.0 MPa and a temperature of 350°C. The weight ratio of ammonia to ethanolamine is The ratio is 12:...
PUM
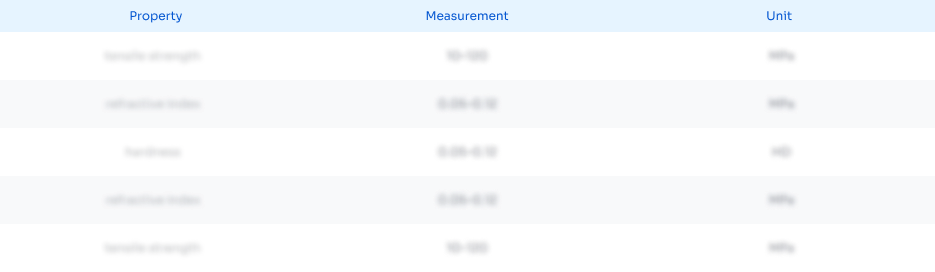
Abstract
Description
Claims
Application Information

- Generate Ideas
- Intellectual Property
- Life Sciences
- Materials
- Tech Scout
- Unparalleled Data Quality
- Higher Quality Content
- 60% Fewer Hallucinations
Browse by: Latest US Patents, China's latest patents, Technical Efficacy Thesaurus, Application Domain, Technology Topic, Popular Technical Reports.
© 2025 PatSnap. All rights reserved.Legal|Privacy policy|Modern Slavery Act Transparency Statement|Sitemap|About US| Contact US: help@patsnap.com