Method of preparing metal casing
A technology for metal shells and manufacturing methods, applied to metal shells, manufacturing tools, metal processing equipment, etc., can solve the problems of high processing costs, increased metal shell volume, long processing time, etc., achieve good mechanical properties, improve The effect of shortening the production efficiency and molding time
- Summary
- Abstract
- Description
- Claims
- Application Information
AI Technical Summary
Problems solved by technology
Method used
Image
Examples
Embodiment Construction
[0013] The preferred embodiment of the present invention discloses a method for manufacturing a metal shell, which is suitable for shells of electronic devices such as mobile phones, PDAs, MP3s, and palmtop computers, and the thickness of the middle and surrounding sides of the metal shell to be formed is different. etc., the following molding method will be described by taking the surrounding thickness of the metal shell greater than the middle thickness as an example.
[0014] The manufacturing method of the metal casing described in this preferred embodiment includes the following steps:
[0015] cutting. see figure 1 , cutting out a plate blank 20 on a plate according to the shape and size of the shell. In this embodiment, the blank 20 is made of aluminum alloy. It can be understood that the material of the blank 20 is also other metal materials, such as magnesium alloy.
[0016] Roll forming. see Figure 2 to Figure 4 , use the rolling mold 30 to carry out rolling f...
PUM
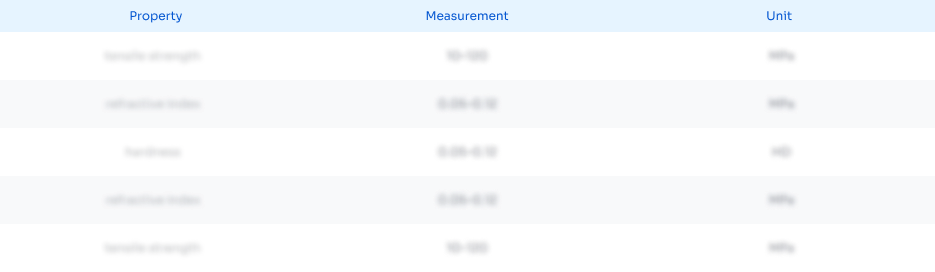
Abstract
Description
Claims
Application Information

- R&D Engineer
- R&D Manager
- IP Professional
- Industry Leading Data Capabilities
- Powerful AI technology
- Patent DNA Extraction
Browse by: Latest US Patents, China's latest patents, Technical Efficacy Thesaurus, Application Domain, Technology Topic, Popular Technical Reports.
© 2024 PatSnap. All rights reserved.Legal|Privacy policy|Modern Slavery Act Transparency Statement|Sitemap|About US| Contact US: help@patsnap.com