Preparation method for synthesizing brominated polycarbonate
A technology of brominated polycarbonate and double catalyst is applied in the preparation of flame retardant brominated polycarbonate and the preparation of double catalyst to synthesize brominated polycarbonate, which can solve the problems of low catalytic efficiency of a single catalyst and achieve control The effect of production cost, high efficiency and simple process
- Summary
- Abstract
- Description
- Claims
- Application Information
AI Technical Summary
Problems solved by technology
Method used
Image
Examples
Embodiment 1
[0036] (1) catalyzer triethylamine 0.84ml (0.006mol) is dissolved in 40ml dichloroethane, standby;
[0037] (2) Add 100g (0.184mol) of tetrabromobisphenol A, 150ml of water, 15g (0.375mol) of sodium hydroxide, 140ml of dichloroethane, 22.9g (0.077mol) of triphosgene into the reaction vessel, stir for 35min, and dissolve. Keep at 20-25°C;
[0038] (3) Add the solution prepared in step (1) dropwise to the reaction system, 5.44ml (0.009mol) of dibutyltin dilaurate, and stir for 60min;
[0039] (4) Dissolve 8g (0.2mol) of sodium hydroxide and 8.64g (0.092mol) of phenol in 142ml of water, slowly add the dissolved mixed solution into the reaction system, and stir and react at 30-35°C for 150min;
[0040] (5) Wash with 50 ml of 1% sodium hydroxide, let stand to separate layers, and separate the organic layer;
[0041] (6) wash with 50ml of 1% hydrochloric acid, leave to stand for stratification, and separate the organic layer;
[0042] (7) Wash with 150ml of deionized water three ...
Embodiment 2
[0047] (1) Dissolve 0.84ml (0.006mol) of catalyst triethylamine in 40ml of dichloroethane for later use; (2) add 100g (0.184mol) of tetrabromobisphenol A, 150ml of water, and 15.2g of sodium hydroxide into the reaction vessel (0.38mol), dichloroethane 140ml, triphosgene 24.04g (0.081mol), stir for 35min, dissolve, keep at 20-25°C;
[0048] (3) Add the solution prepared in step (1) dropwise to the reaction system, 5.44ml (0.009mol) of dibutyltin dilaurate, and stir for 60min;
[0049] (4) Dissolve 8.8g (0.22mol) of sodium hydroxide and 9.504g (0.101mol) of phenol in 142ml of water, slowly add the dissolved mixture dropwise into the reaction system, and stir and react at 30-35°C for 150min;
[0050] (5) Wash with 50 ml of 1% sodium hydroxide, let stand to separate layers, and separate the organic layer;
[0051] (6) Wash with 50ml of 1% hydrochloric acid, leave to stand for stratification, and separate the organic phase;
[0052] (7) Wash with 150ml of deionized water for thre...
Embodiment 3
[0057] (1) catalyzer triethylamine 0.84ml (0.006mol) is dissolved in 40ml dichloroethane, standby;
[0058] (2) Add 100g (0.184mol) of tetrabromobisphenol A, 150ml of water, 14.72g (0.368mol) of sodium hydroxide, 140ml of dichloroethane, 22.4g (0.075mol) of triphosgene into the reaction vessel, stir for 35min, dissolve , keep at 20-25°C;
[0059] (3) Add the solution prepared in step (1) dropwise to the reaction system, 5.44ml (0.009mol) of dibutyltin dilaurate, and stir for 60min;
[0060] (4) Dissolve 7.0g (0.175mol) of sodium hydroxide and 7.52g (0.08mol) of phenol in 142ml of water, slowly add the dissolved mixture dropwise into the reaction system, and stir and react at 30-35°C for 150min;
[0061] (5) Wash with 50 ml of 1% sodium hydroxide, let stand to separate layers, and separate the organic layer;
[0062] (6) Wash with 50ml of 1% hydrochloric acid, leave to stand for stratification, and separate the organic phase;
[0063] (7) Wash with 150ml of deionized water f...
PUM
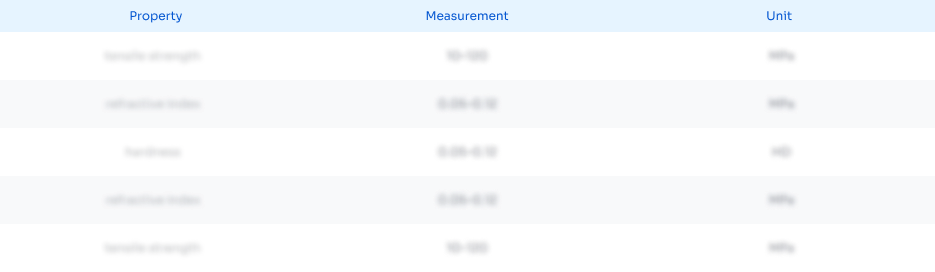
Abstract
Description
Claims
Application Information

- R&D Engineer
- R&D Manager
- IP Professional
- Industry Leading Data Capabilities
- Powerful AI technology
- Patent DNA Extraction
Browse by: Latest US Patents, China's latest patents, Technical Efficacy Thesaurus, Application Domain, Technology Topic, Popular Technical Reports.
© 2024 PatSnap. All rights reserved.Legal|Privacy policy|Modern Slavery Act Transparency Statement|Sitemap|About US| Contact US: help@patsnap.com