Method for manufacturing composite particle fertilizer by employing straw slurry paper-making waste
A manufacturing method and a technology of composite particles, which are applied in the field of paper pulping waste to make compound fertilizers, can solve problems such as straw pulping pollution, and achieve the effects of solving pollution problems and optimizing utilization effects
- Summary
- Abstract
- Description
- Claims
- Application Information
AI Technical Summary
Problems solved by technology
Method used
Examples
Embodiment 1
[0021] (1) The rice straw raw material is pulped with ammonium sulfite and urea. After cooking, the waste liquid is extracted with a twin-screw squeezer. The solid content of the waste liquid is 12.5%.
[0022] (2) Pour the pulping waste liquid into the reaction kettle, feed in oxygen, and the pressure is 1.0Mpa; the temperature is raised to 100°C; the reaction time is 90min. Increase the organic nitrogen content of waste liquid from 1.2% to 4.8% by oxidative ammonolysis reaction
[0023] (3) Use a 5-effect evaporator to increase the concentration of waste liquid from oxidative ammonium hydrolysis from 12.5% to 38%.
[0024] (4) Use pulverizer to pulverize the grass powder of rice straw preparation, pass through 30 mesh sieves, use the flue gas of boiler to dry to 90% dryness.
[0025] (5) Use a ball mill to pulverize the ash and fly ash of the power boiler, pass through a 40-mesh sieve, and dry to a dryness of 90%.
[0026] (6) Mix power boiler ash: grass powder: waste li...
Embodiment 2
[0030] (1) The rice straw raw material is pulped with ammonium sulfite and urea. After cooking, the waste liquid is extracted with a twin-screw squeezer. The solid content of the waste liquid is 13.1%.
[0031] (2) Pour the pulping waste liquid into the reaction kettle, feed in oxygen, and the pressure is 0.9Mpa; the temperature is raised to 105°C; the reaction time is 85min. Increase the organic nitrogen content of waste liquid from 1.2% to 4.5% by oxidative ammonolysis reaction
[0032] (3) Use a 5-effect evaporator to increase the concentration of waste liquid from oxidative ammonium hydrolysis from 13.1% to 40%.
[0033] (4) Use pulverizer to pulverize the grass powder of rice straw preparation, pass through 30 mesh sieves, use the flue gas of boiler to dry to 90% dryness.
[0034] (5) Use a ball mill to pulverize the ash and fly ash of the power boiler, pass through a 40-mesh sieve, and dry to a dryness of 90%.
[0035] (6) Mix the power boiler ash:grass powder:waste li...
Embodiment 3
[0039] (1) The rice straw raw material is pulped with ammonium sulfite and urea. After cooking, the waste liquid is extracted with a twin-screw squeezer. The solid content of the waste liquid is 11.4%.
[0040] (2) Pour the pulping waste liquid into the reaction kettle, feed in oxygen, and the pressure is 1.1Mpa; the temperature is raised to 95°C; the reaction time is 100min. Increase the organic nitrogen content of waste liquid from 1.2% to 4.6% by oxidative ammonolysis reaction
[0041] (3) Use a 5-effect evaporator to increase the concentration of waste liquid from oxidative ammonium hydrolysis from 11.4% to 38%.
[0042] (4) Use pulverizer to pulverize the grass powder of rice straw preparation, pass through 30 mesh sieves, use the flue gas of boiler to dry to 90% dryness.
[0043] (5) Use a ball mill to pulverize the ash and fly ash of the power boiler, pass through a 40-mesh sieve, and dry to a dryness of 90%.
[0044] (6) Mix power boiler ash: grass powder: waste liqu...
PUM
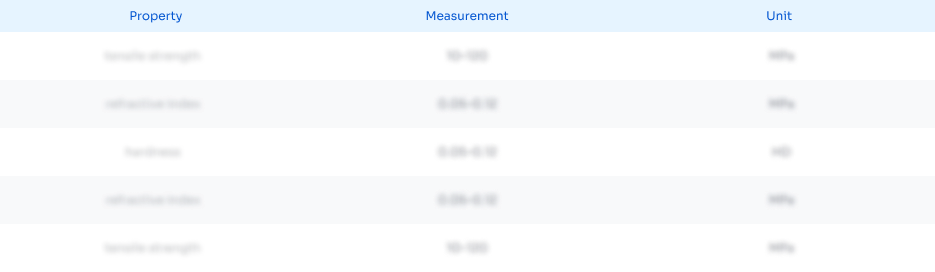
Abstract
Description
Claims
Application Information

- Generate Ideas
- Intellectual Property
- Life Sciences
- Materials
- Tech Scout
- Unparalleled Data Quality
- Higher Quality Content
- 60% Fewer Hallucinations
Browse by: Latest US Patents, China's latest patents, Technical Efficacy Thesaurus, Application Domain, Technology Topic, Popular Technical Reports.
© 2025 PatSnap. All rights reserved.Legal|Privacy policy|Modern Slavery Act Transparency Statement|Sitemap|About US| Contact US: help@patsnap.com