Calcification vanadium slag sintering method
A technology for calcification roasting and vanadium slag is applied in the field of calcification roasting vanadium slag, which can solve the problems of no patents or reports on vanadium-containing materials, and achieve the effects of shortening roasting time, easy temperature control, and improving production capacity.
- Summary
- Abstract
- Description
- Claims
- Application Information
AI Technical Summary
Problems solved by technology
Method used
Examples
Embodiment 1
[0015] Roasting experiment of embodiment 1 vanadium slag in muffle furnace
[0016] Vanadium slag (containing V 2 o 5 15.43%, CaO<0.5%) crushed to pass through a 0.1mm sieve. Take 100g of crushed vanadium slag, add 7.72g of lime, mix well and put it in a porcelain crucible for use.
[0017] The temperature of the muffle furnace was raised to 900°C and kept at a constant temperature. Put the prepared vanadium slag mixture into the muffle furnace, take it out after 60 minutes and cool it to room temperature. Crush the roasted clinker until it passes through a 40-mesh sieve, take 80g of clinker and add 320ml of water to make a slurry, then add sulfuric acid with a concentration of 32% to adjust the pH of the solution, keep the pH value of the leaching process at 2.8-3.3, and leaching for 1h Finally, filter the solution, wash the residue 5 times, dry, weigh and analyze the vanadium content of the residue. The conversion rate of vanadium in vanadium slag is 88.95%.
Embodiment 2
[0018] Roasting experiment of embodiment 2 vanadium slag in rotary tube
[0019] Vanadium slag (containing V 2 o 5 16.7%, CaO<0.5%) crushed to pass through a 0.1mm sieve. The crushed vanadium slag and lime were prepared in a weight ratio of 100:9.5 to obtain a 2kg sample, and mixed evenly.
[0020] Raise the temperature of the Ф100×1200mm two-section temperature-controlled rotary tube to 600°C at the rear and 950°C at the front and keep it constant. Add the prepared sample above from the tail of the rotary tube, and control the rotation speed and inclination of the rotary tube so that the average residence time of the vanadium slag in the furnace tube is 50-60 minutes. After the baked clinker is cooled to room temperature, it is crushed to pass through a 40-mesh sieve. Take 1.8kg of the roasted clinker and make a slurry with 3600mL of water. After leaching for 1 hour, filter the solution, wash the residue with water for 5 times, dry, weigh and analyze the vanadium content...
Embodiment 3
[0021] Example 3 High-calcium vanadium slag roasting experiment in fluidized furnace
[0022] A high-calcium vanadium slag directly blown, its V 2 o 5 The CaO content is 14.3%, and the CaO content is 8.86%. The vanadium slag is ground until it passes through a 0.1mm sieve.
[0023] Take 100kg of crushed high-calcium vanadium slag and roast it in a fluidized fluidized furnace of Ф100×2500mm, feed the material from the upper part and discharge the roasted clinker from the lower part, control the average temperature in the fluidized fluidized furnace to 900 °C, and control the average temperature of the vanadium slag in the fluidized fluidized furnace. The residence time is 30min. The roasted clinker released from the oven is crushed to pass through a 40-mesh sieve, 10kg of the roasted clinker is taken, and after being adjusted into a slurry with 30L of water, sulfuric acid with a concentration of 63% is added to adjust the pH of the solution to keep the pH value of the leachi...
PUM
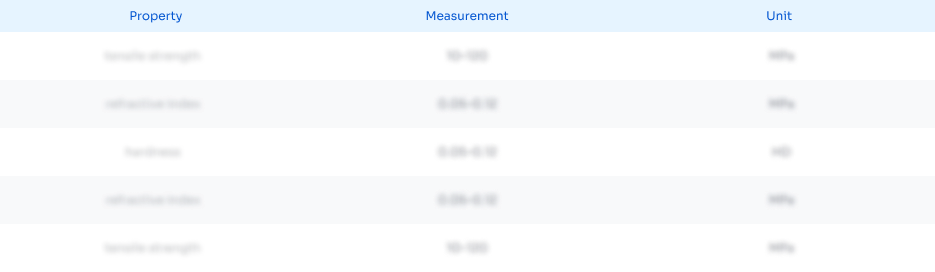
Abstract
Description
Claims
Application Information

- Generate Ideas
- Intellectual Property
- Life Sciences
- Materials
- Tech Scout
- Unparalleled Data Quality
- Higher Quality Content
- 60% Fewer Hallucinations
Browse by: Latest US Patents, China's latest patents, Technical Efficacy Thesaurus, Application Domain, Technology Topic, Popular Technical Reports.
© 2025 PatSnap. All rights reserved.Legal|Privacy policy|Modern Slavery Act Transparency Statement|Sitemap|About US| Contact US: help@patsnap.com