Magnesium desulphurization method for molten iron pretreatment and powder used thereby
A technology of molten iron pretreatment and desulfurization accelerator, applied in the field of iron and steel metallurgy, can solve the problems of lime powder splashing, personal accident, unsatisfactory effect, etc.
- Summary
- Abstract
- Description
- Claims
- Application Information
AI Technical Summary
Problems solved by technology
Method used
Image
Examples
Embodiment 1
[0044] Implement the molten iron pretreatment method that this invention completes on the 150 tons of molten iron ladle of A iron and steel enterprise, iron temperature (in the ladle) 1350 ℃, adopt composite injection powder technology. The chemical composition of the pre-melted magnesium desulfurization accelerator used is shown in Table 3:
[0045] Chemical composition of premelted magnesium desulfurization accelerator 2 Table 3
[0046] ingredient name
[0047] Fluidized pre-melted magnesium desulfurization accelerator is mixed with metal magnesium in a mixing ratio of 3:1. After the mixed powder is prepared, it is sprayed into molten iron. The test results count 100 bags, and the average original sulfur content of molten iron is 0.035%. , the average injection time is 10min; the powder dosage is 2.0kg / t; the average temperature drop is 13°C; the sampling analysis [S] average is 0.003%; No large-scale splashing occurs; it is obviously better than lime-based powde...
Embodiment 2
[0049] Implement the molten iron pretreatment method that this invention completes on the 150 tons of molten iron ladle of A iron and steel enterprise, iron temperature (in the ladle) 1350 ℃, adopt composite injection powder technology. The chemical composition of the pre-melted magnesium desulfurization accelerator used is shown in Table 4:
[0050] Chemical composition of premelted magnesium desulfurization accelerator 2 Table 4
[0051] ingredient name
[0052] Fluidized pre-melted magnesium desulfurization accelerator is mixed with metal magnesium in a mixing ratio of 3:1. After the mixed powder is prepared, it is sprayed into molten iron. The test results count 100 bags, and the average original sulfur content of molten iron is 0.035%. , the average injection time is 10min; the powder dosage is 2.0kg / t; the average temperature drop is 13°C; the sampling analysis [S] average is 0.003%; No large-scale splashing occurs; it is obviously better than lime-based powde...
Embodiment 3
[0054] Implement the molten iron pretreatment method that this invention completes on the 150 tons of molten iron ladle of A iron and steel enterprise, iron temperature (in the ladle) 1350 ℃, adopt composite injection powder technology. The chemical composition of the pre-melted magnesium desulfurization accelerator used is shown in Table 5:
[0055] Chemical composition of premelted magnesium desulfurization accelerator 2 Table 5
[0056] ingredient name
[0057] Fluidized pre-melted magnesium desulfurization accelerator is mixed with metal magnesium in a mixing ratio of 3:1. After the mixed powder is prepared, it is sprayed into molten iron. The test results count 100 bags, and the average original sulfur content of molten iron is 0.035%. , the average injection time is 10min; the powder dosage is 2.0kg / t; the average temperature drop is 13°C; the sampling analysis [S] average is 0.003%; No large-scale splashing occurs; it is obviously better than lime-based powde...
PUM
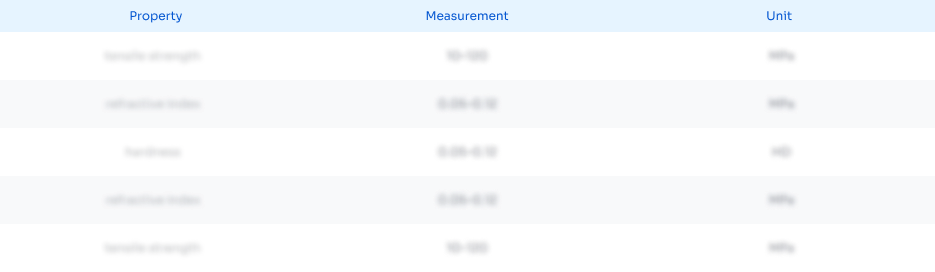
Abstract
Description
Claims
Application Information

- R&D
- Intellectual Property
- Life Sciences
- Materials
- Tech Scout
- Unparalleled Data Quality
- Higher Quality Content
- 60% Fewer Hallucinations
Browse by: Latest US Patents, China's latest patents, Technical Efficacy Thesaurus, Application Domain, Technology Topic, Popular Technical Reports.
© 2025 PatSnap. All rights reserved.Legal|Privacy policy|Modern Slavery Act Transparency Statement|Sitemap|About US| Contact US: help@patsnap.com