Protection package film filling material and preparation method thereof
A technology for packaging films and minerals, applied in the field of protective packaging materials, can solve the problems of immature inorganic antibacterial methods, etc., and achieve the effects of low price, low production cost and low energy consumption
- Summary
- Abstract
- Description
- Claims
- Application Information
AI Technical Summary
Problems solved by technology
Method used
Examples
Embodiment 1
[0018] Take 10g of montmorillonite, soak it in 100ml of water for 48h, add 0.3g of cetyltrimethylammonium bromide modifier and 2ml of 0.1ml / l hydrochloric acid, grind it in a planetary ball mill for 2 hours, add 0.1g of ZnCl 2 Then continue ball milling to nanometer scale. The ball-milled montmorillonite is subjected to solid-liquid separation through a centrifuge; the supernatant is removed, and the precipitate is dried at 100°C to obtain a layered modified nano-aluminosilicate. Take 7g of nano-aluminosilicate, 4g of copper micropowder, and 40g of low-density polyethylene powder, mix them, and add them into a plastic mixer for mixing. The mixing temperature is 170° C., and the plastic mixer speed is 40 rpm. The mixing time is 30 minutes to obtain a uniformly mixed composite masterbatch, which is then passed through a film-making machine to obtain a protective packaging film.
Embodiment 2
[0020] Take 10g of purified and pulverized mica, mechanically grind it for 4 hours in an aqueous medium with a solid-to-liquid ratio of 1:10, add a modifier triethanolamine according to the mica mass ratio of 1.5%, continue to grind to the nanometer level, and separate the solid and liquid by a centrifuge , remove the supernatant, dry the precipitate at 100°C to obtain aluminosilicate powder, take 5g of nano-aluminosilicate powder, 1g of zinc powder, 1g of flake graphite powder, and 30g of linear low-density polyethylene powder and mix evenly. Mix the mixture in a kneader at 170°C for 30 minutes, the speed of the kneader is 40 rpm to obtain a uniformly mixed composite masterbatch, and then pass through a film-making machine to obtain a protective packaging film.
Embodiment 3
[0022] Take 10 g of purified and pulverized kaolinite powder, ball mill it in an aqueous medium with a solid:liquid ratio of 1.5:10 for 4 hours, add 0.2 ml of modifier triethanolamine, continue to grind to the nanometer level, and separate the solid and liquid through a centrifuge. The supernatant was removed, and the precipitate was dried at 100°C to obtain the modified aluminosilicate micropowder. Take 3g of modified kaolinite powder, 1g of iron micropowder, and 1g of carbon powder and mix them evenly. Take 30g of linear low-density polyethylene powder and mix them evenly. Mix the mixture in a mixer at 170°C for 30 minutes. The speed of the mixer is 40 revolutions per minute to prepare a uniformly mixed film masterbatch, and then pass through a film-making machine to obtain a protective packaging film.
PUM
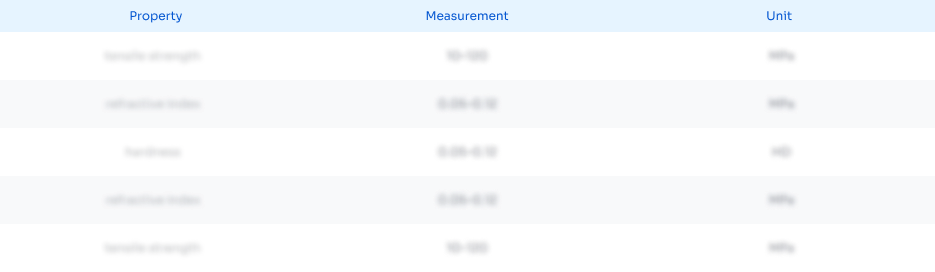
Abstract
Description
Claims
Application Information

- Generate Ideas
- Intellectual Property
- Life Sciences
- Materials
- Tech Scout
- Unparalleled Data Quality
- Higher Quality Content
- 60% Fewer Hallucinations
Browse by: Latest US Patents, China's latest patents, Technical Efficacy Thesaurus, Application Domain, Technology Topic, Popular Technical Reports.
© 2025 PatSnap. All rights reserved.Legal|Privacy policy|Modern Slavery Act Transparency Statement|Sitemap|About US| Contact US: help@patsnap.com