Wood multi-layer floor composed of cut-plate and veneer and method for making same
A technology for a solid wood composite floor and a production method, which is applied in the direction of manufacturing tools, wood processing appliances, floors, etc., can solve the problems of increasing processes and increasing costs, and achieves the effects of improving product quality, low cost, and reducing production costs.
- Summary
- Abstract
- Description
- Claims
- Application Information
AI Technical Summary
Problems solved by technology
Method used
Image
Examples
Embodiment 1
[0060] Embodiment 1: As shown in Figure 1, this is the 7-layer solid wood composite floor based on eucalyptus rotary-cut veneer that is actually designed in a certain wood industry in combination with eucalyptus plywood production. Surface layer 1 is made of 1.6mm thick southwest birch sliced veneer, core layer 2 is made of 6.0mm thick eucalyptus cut board, and bottom layer 3 and 4, 5, 6, and 7 layers are all made of 1.6mm thick eucalyptus rotary cut veneer. The eucalyptus, rotary cut veneer and cut board are all produced by ourselves, and the southwest birch cut veneer is purchased from Yunnan.
[0061] Newly felled eucalyptus, after sawing, peeling, centering, rotary cutting, shearing, air drying, roller drying, and sorting: good ones are used as the bottom layer 3, and slightly inferior ones are used as the middle layer 4, 5, 6, and 7. Finished and used for gluing assembly.
[0062] Newly felled large-diameter eucalyptus, after sawing, sectioning, truncating, and cutting...
Embodiment 2
[0065] Embodiment 2: as shown in Figure 2, select thick 1.8mm southwestern birch sliced veneer for use as surface layer 1, use thick 6.0mm pine cut board as core layer 2, use thick 1.8mm pine rotary cut veneer as bottom layer 3 and The middle 4 or 5 floors. If the pine board used as the core layer needs to be degreased, NaOH lye with a concentration of 0.5-1.2% can be used in the steaming treatment tank at a temperature of 110-120°C, that is, a steam pressure of 1.5-2.0kg / cm 2 Next, cook for 2 hours, then release the lye to the storage pool, the lye can be recycled for use, and the boards are cut at an appropriate temperature, dried, aged, and thickened. Drying, shearing, sorting and sorting for veneers with 4 and 5 layers, double-sided gluing: aging, billet formation, pre-pressing, hot pressing, humidity and temperature adjustment, surface sanding, tenon and groove processing, finishing, sorting etc., packaging, and finished products.
[0066] The structure of this produc...
Embodiment 3
[0068] Embodiment 3: As shown in Figure 3, it is a 3-layer solid wood composite floor, which has the same structure as the thick-core 3-layer plywood. Select the sliced veneer of Southwestern Birch with a thickness of 2.0mm as the surface layer 1, and use the 6.0mm thick pine cut board as the core layer 2. If the pine board needs to be degreased, the treatment process is the same as that of Example 2, and use the 2.0mm thick pine rotary cut veneer Make bottom 3. Glue the core cutting board. In order to make the overall board surface of the product have a certain supporting strength, the core layer cut board is coated with glue on three sides, first with a single roller coating on the side, and then on both sides. Other production process is identical with embodiment 2.
[0069] Slab thickness: 2.0×2+6.0=10.0mm. The product format can be selected arbitrarily according to the needs of users, and can also be made into 4 1 ×8 1 plate. In order to make full use of the lengt...
PUM
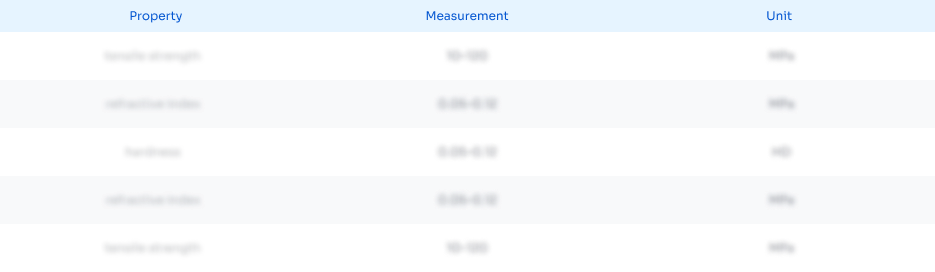
Abstract
Description
Claims
Application Information

- R&D
- Intellectual Property
- Life Sciences
- Materials
- Tech Scout
- Unparalleled Data Quality
- Higher Quality Content
- 60% Fewer Hallucinations
Browse by: Latest US Patents, China's latest patents, Technical Efficacy Thesaurus, Application Domain, Technology Topic, Popular Technical Reports.
© 2025 PatSnap. All rights reserved.Legal|Privacy policy|Modern Slavery Act Transparency Statement|Sitemap|About US| Contact US: help@patsnap.com