Method for welding electric machine rotor copper bar coil by using high-frequency soldering machine
A high-frequency brazing and welding technology, applied in welding/welding/cutting items, welding media, welding equipment, etc., can solve the problems of uneven copper bar surface, cracks at corners, poor electrical conductivity, etc. The effect of good shape, energy saving and high welding efficiency
- Summary
- Abstract
- Description
- Claims
- Application Information
AI Technical Summary
Problems solved by technology
Method used
Image
Examples
Embodiment Construction
[0050] Embodiments of the present invention will be further described below in conjunction with the accompanying drawings.
[0051] The invention provides a welding method for welding the copper bar coils of the motor rotor with a high-frequency brazing machine. The invention completes the welding of the copper bar coils of the motor rotor on the high-frequency brazing machine. The structure proceeds as stated:
[0052] As shown in Figures 1 to 6, the high-frequency brazing machine for welding the copper bar coils of the motor rotor includes: a base 10 with double guide rails 1, a main frame 20, a mobile frame 22, an induction brazing mechanism 30, a workbench and fixtures 100.
[0053] The bottom of the main frame 20 is provided with a drive mechanism 2 to move along the guide rail 1, the drive mechanism 2 is composed of a lead screw 4 connected to the motor 3 and a nut 6 mounted on the lead screw 4 at the bottom of the main frame 20, A slideway 26 parallel to the guide rai...
PUM
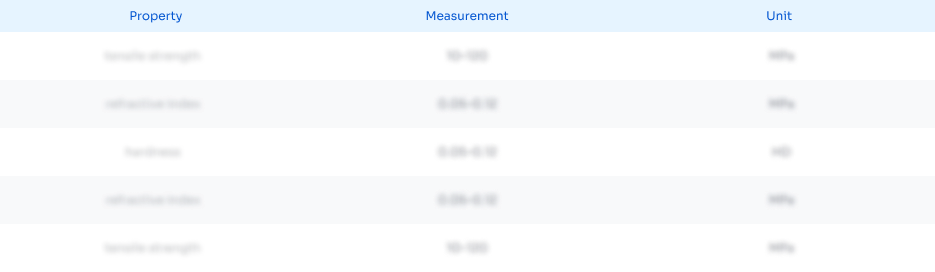
Abstract
Description
Claims
Application Information

- R&D
- Intellectual Property
- Life Sciences
- Materials
- Tech Scout
- Unparalleled Data Quality
- Higher Quality Content
- 60% Fewer Hallucinations
Browse by: Latest US Patents, China's latest patents, Technical Efficacy Thesaurus, Application Domain, Technology Topic, Popular Technical Reports.
© 2025 PatSnap. All rights reserved.Legal|Privacy policy|Modern Slavery Act Transparency Statement|Sitemap|About US| Contact US: help@patsnap.com