Wheel tooth surface electrolyzing precision-processing method and wheel tooth surface precision-processing device
A technology of electrolytic finishing and gear teeth, which is applied in the field of gear tooth surface processing, can solve the problems of high grinding cost, high processing difficulty, and low gear production efficiency, and achieve the goal of improving processing efficiency and quality and reducing processing costs Effect
- Summary
- Abstract
- Description
- Claims
- Application Information
AI Technical Summary
Problems solved by technology
Method used
Image
Examples
Embodiment Construction
[0010] The present invention will be further described below in conjunction with the accompanying drawings and specific embodiments, so as to help understand the content of the present invention.
[0011] As shown in Figure 1, it is a schematic structural diagram of a gear tooth surface finishing device. It includes a first gear support shaft 1 on which a shaving cutter 4 is installed, a second gear support shaft 2 for installing a processed gear 5, and a third gear support shaft 3 on which a standard gear 6 is installed, and makes the processed gear 5 It meshes with the standard gear 6 and the shaving cutter 4. On the standard gear 6, a mesh insulating layer (omitted in the figure) with a thickness of about 0.2mm is evenly arranged on the standard gear 6, so that the metal surfaces of the two will not be in direct contact to avoid short circuits. It can also pass through the electrolyte. The first gear support shaft 1 is the driving shaft, the second gear support shaft 2 and...
PUM
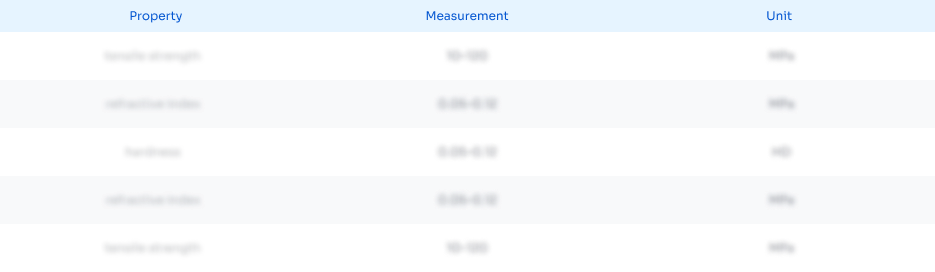
Abstract
Description
Claims
Application Information

- R&D Engineer
- R&D Manager
- IP Professional
- Industry Leading Data Capabilities
- Powerful AI technology
- Patent DNA Extraction
Browse by: Latest US Patents, China's latest patents, Technical Efficacy Thesaurus, Application Domain, Technology Topic, Popular Technical Reports.
© 2024 PatSnap. All rights reserved.Legal|Privacy policy|Modern Slavery Act Transparency Statement|Sitemap|About US| Contact US: help@patsnap.com