Variable-speed gear structure of casting finishing machine tool
A technology of variable speed gears and variable speed mechanisms, which is applied to metal processing equipment, parts of grinding machine tools, grinding machines, etc., can solve problems such as inconvenient adjustment, low work efficiency, and poor grinding quality, so as to achieve convenient operation and improve grinding processing Quality, the effect of improving processing efficiency and quality
- Summary
- Abstract
- Description
- Claims
- Application Information
AI Technical Summary
Problems solved by technology
Method used
Image
Examples
Embodiment 1
[0023] Embodiment one: refer to Figure 1~3 , in an embodiment of the present invention, a casting finishing machine tool speed change gear structure, including a base 20 and a transmission shaft 8 connected to the output end of the motor, a speed change mechanism 1 is placed on the upper part of the base 20, to achieve multi-speed adjustment, control processing, close to The upper part of the base 20 of the transmission mechanism 1 is equipped with a cooling water tank 19, and the side end of the cooling water tank 19 is connected with a cooling water pipe 18, which is convenient for cooling the cutting part, and the cooling water can be recycled to save resources. 8 is provided with a driving bevel gear 9, the driving bevel gear 9 meshes with a driven bevel gear 10, the output end of the driven bevel gear 10 is connected to a crank shaft 11, and the crank shaft 11 is connected to a transmission rod 12 for rotation, and the transmission rod 12 is fixed. Connected on the conne...
Embodiment 2
[0030] Embodiment 2: The invention also provides another embodiment, which is improved on the basis of the above-mentioned embodiment. The support frame 7 is provided with a through groove 13, and the width of the through groove 13 is larger than that of the transmission The thickness of the rod 12 avoids interfering with the movement of the transmission rod 12.
[0031] In summary, when the invention works, the casting 21 is clamped and fixed by the fixed support one 3 and the fixed support two 14, which is convenient to operate and is suitable for castings 21 of different sizes. At this time, the transmission shaft 8 under the motor drive Under the transmission of the driving gear 5, the driven gear 6 and the gear ring 22, the rotation direction of the casting 21 and the grinding knife 4 is opposite, greatly improving the machining efficiency and quality of the grinding knife 4 cutting the inner wall of the casting 21, and, by Under the transmission of the active bevel gear ...
PUM
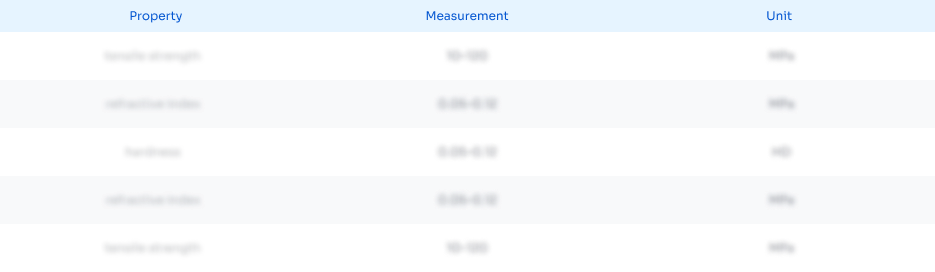
Abstract
Description
Claims
Application Information

- R&D
- Intellectual Property
- Life Sciences
- Materials
- Tech Scout
- Unparalleled Data Quality
- Higher Quality Content
- 60% Fewer Hallucinations
Browse by: Latest US Patents, China's latest patents, Technical Efficacy Thesaurus, Application Domain, Technology Topic, Popular Technical Reports.
© 2025 PatSnap. All rights reserved.Legal|Privacy policy|Modern Slavery Act Transparency Statement|Sitemap|About US| Contact US: help@patsnap.com