Nickel zinc ferrite low temperature high density production method and its product
A technology of nickel-zinc ferrite and manufacturing method, which is applied in the direction of magnetism of inorganic materials, can solve the problems of lowering the Curie temperature and deterioration of characteristics, and achieve the effects of high Curie temperature, high magnetic permeability, and high saturation magnetic induction intensity
- Summary
- Abstract
- Description
- Claims
- Application Information
AI Technical Summary
Problems solved by technology
Method used
Image
Examples
Embodiment Construction
[0023] 47.5~49.5mol% Fe 2 o 3 , 3.6-6.5mol% of CuO, 30-35mol% of ZnO, and the rest are the main components of NiO. After mixing, pre-calcine, add 0.01-0.4wt% of Ti 2 o 5 , 0.01~0.5wt% Bi 2 o 3 , 0.01~0.5wt% V 2 o 5 , 0.01~0.5wt% MoO 3 , 0.01~0.5wt% Cr 2 o 3 , 0.01~0.5wt% Nb 2 o 5 At least one of the auxiliary components, that is, impurities, is then pulverized, and a small amount of binder PVA is added to make a slurry with a certain viscosity, which is made into 80-220 mesh particles by spray granulation, and then the particles are pressed into the required shape of the finished blank, the blank can be highly densified (5.2g / cm 3 above) finished product.
[0024] Main component shown in table 1 and secondary component are embodiments of the present invention (A, B, C, F, G, I, J), after testing, obtaining density is 5.2g / cm 3 The sintering temperature required for the finished product and the magnetic permeability, saturation magnetic induction and Curie temperat...
PUM
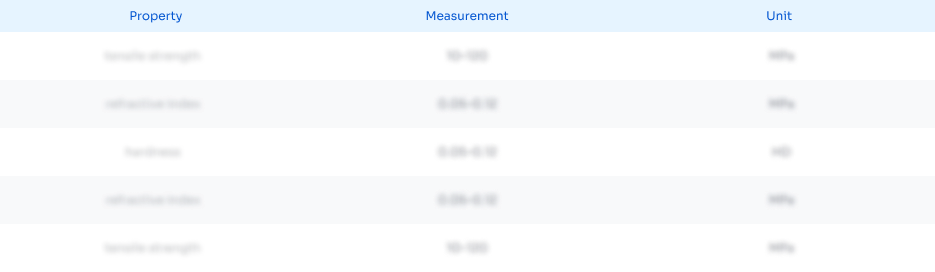
Abstract
Description
Claims
Application Information

- Generate Ideas
- Intellectual Property
- Life Sciences
- Materials
- Tech Scout
- Unparalleled Data Quality
- Higher Quality Content
- 60% Fewer Hallucinations
Browse by: Latest US Patents, China's latest patents, Technical Efficacy Thesaurus, Application Domain, Technology Topic, Popular Technical Reports.
© 2025 PatSnap. All rights reserved.Legal|Privacy policy|Modern Slavery Act Transparency Statement|Sitemap|About US| Contact US: help@patsnap.com