Prepn process of malonic ester
A technology of malonate and cyanoacetic acid, which is applied in the field of malonate preparation, can solve the problems of difficulty in realizing large-scale industrial production, high recovery cost of extractant toluene, large amount of extractant toluene, etc. The effect of reducing the amount of feed to the kettle, low production cost, and reducing the cost of environmental protection treatment
- Summary
- Abstract
- Description
- Claims
- Application Information
AI Technical Summary
Problems solved by technology
Method used
Examples
Embodiment 1
[0020] Embodiment 1: the preparation method of dimethyl malonate, its steps are as follows:
[0021] 725g of industrial chloroacetic acid with a weight percentage content of 98% (calculated as 7.5 moles), add 500g of water to dissolve, stir, and neutralize to pH=6.5~7.0 with aqueous sodium carbonate solution under cooling conditions to obtain sodium chloroacetate aqueous solution.
[0022] Mix the above-mentioned sodium chloroacetate aqueous solution with a liquid sodium cyanide solution with a concentration of 30% by weight, raise the temperature to 50°C, and initiate the cyanation reaction. When the cyanation reaction temperature reaches 85-90°C, stop heating and start cooling. When the cyanidation reaction temperature reached 105-115°C, the reaction was over, and then cooled down to below 60°C to obtain 4000g of sodium cyanoacetate solution, which was sampled and analyzed as CN-qualified. The obtained sodium cyanoacetate solution is divided into 5 equal parts, which are re...
Embodiment 2
[0033] Embodiment 2: the preparation method of diethyl malonate, its steps are as follows:
[0034] With the step in embodiment 1, carry out neutralization reaction and cyanation reaction with industrial chloroacetic acid as raw material, obtain sodium cyanoacetate solution 4170g. The obtained sodium cyanoacetate solution is divided into 5 equal parts, which are respectively used in the circulation reactions of the following circulation 1) to circulation 5).
[0035] Loop 1):
[0036]Get above-mentioned gained sodium cyanoacetate solution 1 / 5 namely 834g, add the industrial hydrochloric acid 185g that weight percentage concentration is 31% and carry out acidification, obtain the mixed aqueous solution of cyanoacetic acid and sodium chloride. Heating and evaporative desalination under vacuum conditions, the temperature is controlled at 60-85°C, when most of the sodium chloride is precipitated, cool to 50°C, filter, and wash the solid sodium chloride with a small amount of wate...
Embodiment 3
[0045] Embodiment 3: the preparation method of diisopropyl malonate, its steps are as follows:
[0046] With the step in embodiment 1, carry out neutralization reaction and cyanation reaction with industrial chloroacetic acid as raw material, obtain sodium cyanoacetate solution 4125g. Gained sodium cyanoacetate solution is divided into 5 equal parts, carries out circulation experiment with the step of embodiment 1, and wherein esterification is replaced methyl alcohol with Virahol (100%) 200g, and all the other are with embodiment 1.
[0047] The experimental data of the above cycles are shown in Table 3.
[0048] cycle batch
PUM
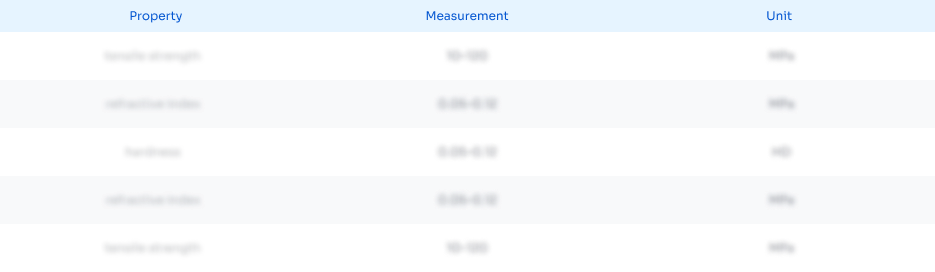
Abstract
Description
Claims
Application Information

- R&D
- Intellectual Property
- Life Sciences
- Materials
- Tech Scout
- Unparalleled Data Quality
- Higher Quality Content
- 60% Fewer Hallucinations
Browse by: Latest US Patents, China's latest patents, Technical Efficacy Thesaurus, Application Domain, Technology Topic, Popular Technical Reports.
© 2025 PatSnap. All rights reserved.Legal|Privacy policy|Modern Slavery Act Transparency Statement|Sitemap|About US| Contact US: help@patsnap.com