Electroplating sludge treating and utilizing process
A technology for electroplating sludge and treatment methods, which is applied in sludge treatment, water/sludge/sewage treatment, dehydration/drying/concentrated sludge treatment, etc. It can solve the problems of inability to realize resource utilization, large energy consumption, and high cost. problems, to achieve the effect of simple and easy purification, improved economic benefits, and high recovery rate
- Summary
- Abstract
- Description
- Claims
- Application Information
AI Technical Summary
Problems solved by technology
Method used
Image
Examples
Embodiment 1
[0075] As shown in Fig. 1, Fig. 2 and Fig. 3: the specific technological process of the novel resource treatment method of electroplating sludge of the present invention is
[0076] A. Alkali addition and roasting: Dry 5 tons of electroplating sludge at a temperature of 100°C, add 0.2 tons of sodium carbonate after drying and roast at a temperature of 400°C for 100 minutes to make Cr 3+ →Cr 6+ After the conversion rate reaches more than 90%, add 4 tons of water, heat to 90 ℃ to leach all soluble metals, and filter through a filter press (manufactured by Hangzhou Chuangyuan Company) to separate the alkali leaching residue and alkali leaching solution; The leaching residue is rinsed with water for 2 to 3 times before use, and the water after rinsing is returned to the above leaching water before leaching;
[0077] B. Refined dichromate: add concentrated sulfuric acid with a concentration of 90% to the alkali immersion solution separated by the above-mentioned pressure filtratio...
Embodiment 2
[0080] As shown in Fig. 1, Fig. 2 and Fig. 3: the specific technological process of the novel resource treatment method of electroplating sludge of the present invention is
[0081] A. Alkali addition and roasting: Dry 5 tons of electroplating sludge at a temperature lower than 100°C. After drying, add 0.2 to 0.3 tons of sodium carbonate and roast at a temperature of 400 to 800°C for 80 minutes to make Cr 3+ →Cr 6+ After the conversion rate reaches over 90%, add 5 tons of water and heat to 92°C to extract Cr +6 , through a filter press (manufactured by Hangzhou Chuangyuan Co., Ltd.) to separate the alkali leaching residue and alkali leaching solution; wherein the alkali leaching residue is rinsed with water for 2 to 3 times and then used, and the water after rinsing is returned to the above-mentioned leaching water;
[0082] B. Refined dichromate: add concentrated sulfuric acid with a concentration of 95% to the alkaline immersion solution separated by the above-mentioned pre...
Embodiment 3
[0085] As shown in Fig. 1, Fig. 2 and Fig. 3: the specific technological process of the novel resource treatment method of electroplating sludge of the present invention is
[0086] A. Alkali addition and roasting: Dry 5 tons of electroplating sludge at a temperature of 100°C, add 0.3 tons of sodium carbonate after drying and roast at a temperature of 800°C for 100 minutes to make Cr 3+ →Cr 6+ After the conversion rate reaches more than 90%, add 6 tons of water, heat to 95° C. to leach all soluble metals, and filter through a plate and frame filter press (manufactured by Hangzhou Chuangyuan Company) to separate the alkali leaching residue and alkali leaching solution; Wherein the alkali leaching residue is rinsed with water for 2 to 3 times before use, and the water after rinsing is returned to the above alkali leaching solution;
[0087] B. Refined dichromate: Add the above-mentioned alkali immersion solution separated by pressure filtration into 98% concentrated sulfuric ac...
PUM
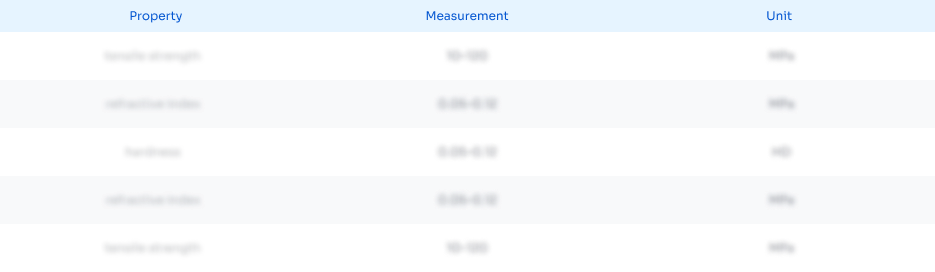
Abstract
Description
Claims
Application Information

- R&D
- Intellectual Property
- Life Sciences
- Materials
- Tech Scout
- Unparalleled Data Quality
- Higher Quality Content
- 60% Fewer Hallucinations
Browse by: Latest US Patents, China's latest patents, Technical Efficacy Thesaurus, Application Domain, Technology Topic, Popular Technical Reports.
© 2025 PatSnap. All rights reserved.Legal|Privacy policy|Modern Slavery Act Transparency Statement|Sitemap|About US| Contact US: help@patsnap.com