Composite material formed of organic polymer and mesoporous molecular sieve and its interface structure and preparation method thereof
A technology of mesoporous molecular sieve and composite material, applied in the field of organic polymer modified composite material and its preparation, achieves the effects of strong adsorption function, large specific surface area, regular and orderly mesoporous channels
- Summary
- Abstract
- Description
- Claims
- Application Information
AI Technical Summary
Problems solved by technology
Method used
Image
Examples
Embodiment 1
[0045] After 3g of silicon-based mesoporous molecular sieve was dried for 2h in a vacuum environment at 200℃ and pressure <0.1MPa, 97g of styrene with 300mg of dibenzoyl peroxide dissolved in it was added to it, and dispersed and infiltrated by ultrasonic waves with a frequency of 59KHz for 30min , Immerse for 60h under vacuum conditions at room temperature and pressure <0.1MPa to obtain a mixture of styrene and molecular sieve. After pre-polymerization for 1.5 hours at 88°C under nitrogen protection with a flow rate of 3ml / min and stirring at a speed of 100rpm, it was cast in a petri dish; then it was further polymerized at 65°C for 18h and treated at 100°C for 2h to make the reaction complete and remove impurities. After the reaction monomers and oligomers are cooled, a polystyrene / mesoporous molecular sieve composite material containing about 3% of the mesoporous molecular sieve is obtained.
Embodiment 2
[0047] After drying 5g of silicon-based mesoporous molecular sieve for 2h in a vacuum environment at 200°C and a pressure of <0.1MPa, add 95g of styrene with 300mg of dibenzoyl peroxide dissolved in it, and disperse and infiltrate with ultrasonic waves at a frequency of 59KHz for 30min. , Immerse for 60h under vacuum conditions at room temperature and pressure <0.1MPa to obtain a mixture of styrene and molecular sieve. After pre-polymerization for 1.5 hours at 88°C under nitrogen protection with a flow rate of 3ml / min and stirring at a speed of 100rpm, it was cast in a petri dish; then it was further polymerized at 65°C for 18h and treated at 100°C for 2h to make the reaction complete and remove impurities. After the reaction monomers and oligomers are cooled, a polystyrene / mesoporous molecular sieve composite material containing about 5% of the mesoporous molecular sieve is obtained.
Embodiment 3
[0049] After 7g of silicon-based mesoporous molecular sieve was dried for 2h in a vacuum environment at 200℃ and pressure <0.1MPa, 300mg of dibenzoyl peroxide dissolved in 93g of styrene was added to it, and dispersed and infiltrated by ultrasonic waves with a frequency of 59KHz for 30min , Immerse for 60h under vacuum conditions at room temperature and pressure <0.1MPa to obtain a mixture of styrene and molecular sieve. After pre-polymerization for 1.5 hours at 88°C under nitrogen protection with a flow rate of 3ml / min and stirring at a speed of 100rpm, it was cast in a petri dish; then it was further polymerized at 65°C for 18h and treated at 100°C for 2h to make the reaction complete and remove impurities. After the reaction monomers and oligomers are cooled, a polystyrene / mesoporous molecular sieve composite material containing about 7% of the mesoporous molecular sieve is obtained.
PUM
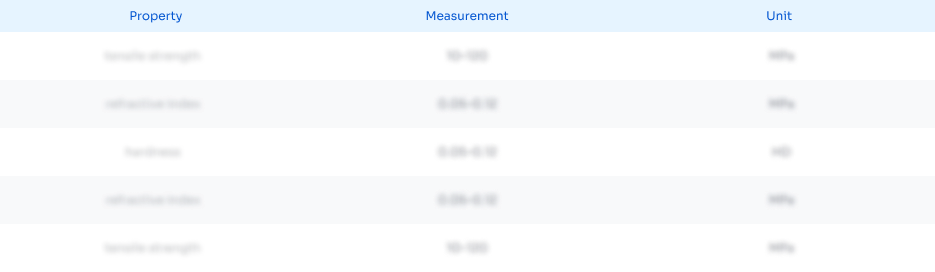
Abstract
Description
Claims
Application Information

- R&D
- Intellectual Property
- Life Sciences
- Materials
- Tech Scout
- Unparalleled Data Quality
- Higher Quality Content
- 60% Fewer Hallucinations
Browse by: Latest US Patents, China's latest patents, Technical Efficacy Thesaurus, Application Domain, Technology Topic, Popular Technical Reports.
© 2025 PatSnap. All rights reserved.Legal|Privacy policy|Modern Slavery Act Transparency Statement|Sitemap|About US| Contact US: help@patsnap.com