Method of producing whole extinction polyester fiber
A technology of polyester fiber and production method, which is applied in the production field of polyester fiber and fully matte polyester fiber, can solve the problem that the content of matting agent TiO2 in fully matt chips is not easy to adjust flexibly, and it is difficult for long-term continuous production of full matt chips, and full matt chips are difficult to produce continuously for a long time. The market demand for slices is not large, and the effect of overcoming spinning difficulties, soft fabric luster and reducing production costs is achieved.
- Summary
- Abstract
- Description
- Claims
- Application Information
AI Technical Summary
Problems solved by technology
Method used
Examples
Embodiment 1
[0014] Melt spinning is carried out by using sheath-core composite spinning components, and the core components are all made of TiO 2 For semi-dull PET slices with a content of 0.2%-0.5%, 97.5% of the cortex components are also the above-mentioned semi-dull PET slices, and the remaining 2.5% are TiO-containing 2 50% of the major Japanese ink companies import full extinction masterbatch, and the total amount of cortex components accounts for 30% of all raw material slices. The spinning process is: chip conveying→drying→masterbatch adding device metering and mixing→screw extruder→melt filter→spinning box→metering pump→spinneret assembly→side blowing→cooling→winding. The spinning temperature is controlled at 290-295° C., and the spinning speed is 3000-4000 m / min to obtain full-dull POY winding yarn. The POY winding wire is further processed into DTY through double-zone thermal stretching, with a draw ratio of 1.58-1.72. The temperature of the deformation heating box is controll...
Embodiment 2
[0016] Same as Example 1, wherein 5.0% of the full matt masterbatch is added to the skin layer component.
Embodiment 3
[0018] Same as Example 1, wherein the total amount of cortex components accounts for 20% of all raw material slices.
PUM
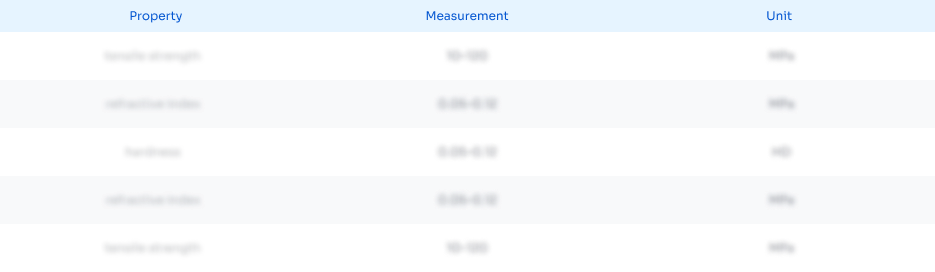
Abstract
Description
Claims
Application Information

- R&D
- Intellectual Property
- Life Sciences
- Materials
- Tech Scout
- Unparalleled Data Quality
- Higher Quality Content
- 60% Fewer Hallucinations
Browse by: Latest US Patents, China's latest patents, Technical Efficacy Thesaurus, Application Domain, Technology Topic, Popular Technical Reports.
© 2025 PatSnap. All rights reserved.Legal|Privacy policy|Modern Slavery Act Transparency Statement|Sitemap|About US| Contact US: help@patsnap.com