High-temperature antifriction metal
A high-temperature anti-wear and alloy technology, applied in the field of alloys, can solve problems such as restricting the development of the aluminum industry and poor maintenance working conditions, and achieve the effect of good high-temperature anti-wear performance and long service life
- Summary
- Abstract
- Description
- Claims
- Application Information
AI Technical Summary
Problems solved by technology
Method used
Examples
Embodiment Construction
[0006] The kiln mouth back iron and the central cylinder are characterized by abrasive impact and friction at high temperature (about 1100°C). On the basis of considering the oxidation resistance, multiple strengthening elements are added to strengthen the austenite matrix and improve the Cr 23 C 6 The morphology and distribution of carbides can improve the high-temperature strength and high-temperature wear resistance of materials. According to the characteristics of alternating oxidation and wear in the failure process of high-temperature wear parts, an appropriate amount of rare earth elements and other elements that strengthen the surface oxide layer are added to make the oxide film and The matrix collectively resists the friction of the abrasive.
[0007] C
Si
mn
P
S
Cr
0.13-0.28%
0.5-2.2%
0.7-1.6%
≤0.04%
≤0.03%
21-25%
Ni
Mo
V
N
Re
Fe
6-8%
0.8-1.2%
0.4-0.7% ...
PUM
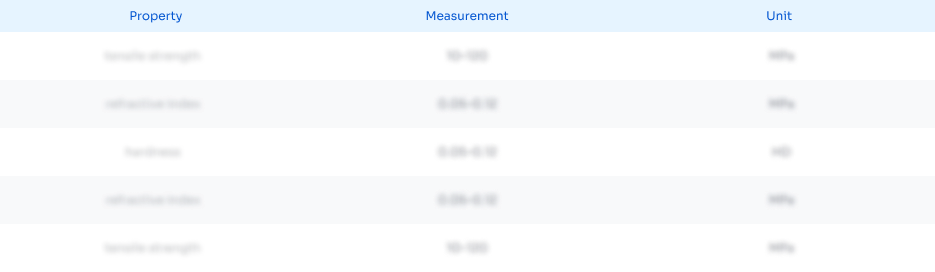
Abstract
Description
Claims
Application Information

- Generate Ideas
- Intellectual Property
- Life Sciences
- Materials
- Tech Scout
- Unparalleled Data Quality
- Higher Quality Content
- 60% Fewer Hallucinations
Browse by: Latest US Patents, China's latest patents, Technical Efficacy Thesaurus, Application Domain, Technology Topic, Popular Technical Reports.
© 2025 PatSnap. All rights reserved.Legal|Privacy policy|Modern Slavery Act Transparency Statement|Sitemap|About US| Contact US: help@patsnap.com