Hydrogenation refined catalyst, preparation method and application
A hydrorefining and catalyst technology, applied in refining to remove heteroatoms, etc., can solve the problem of poor hydrogenation saturated monoolefin activity, inability to adapt to heavy hydrogenation raw materials, and variable sulfur content hydrogenation feedstock oil space velocity Increasingly high market requirements, etc.
- Summary
- Abstract
- Description
- Claims
- Application Information
AI Technical Summary
Problems solved by technology
Method used
Examples
Embodiment 1
[0034] 300g of alumina powder prepared by nitric acid method was added with 18ml of silica sol, 4.3ml of phosphoric acid, and 140ml of water, kneaded and extruded, dried at 120°C in the air, and roasted at 620°C for 4 hours to obtain silicon- and phosphorus-containing Elemental γ-Al 2 o 3 carrier. At 55°C, add 4.3g of cobalt acetate to 5ml of water and stir to dissolve, add 15ml of ammonia water containing 30% ammonia during stirring, add 0.5g of potassium hydroxide, 9.6g of ammonium molybdate, and 2.8g of nickel nitrate while stirring, and stir After dissolving, it was impregnated on 30g carrier, aged for 12 hours, dried at 120°C, and calcined at 480°C for 4 hours to obtain catalyst A.
Embodiment 2
[0038] 300g of alumina powder prepared by nitric acid method, add 14ml of additive silica sol, 6.0ml of phosphoric acid, add 140ml of water, knead and extrude, dry in the air at 100-120°C, and roast at 560°C for 6 hours, the obtained silicon-containing , phosphorus element γ-Al 2 o 3 carrier. At 30°C, add 5.4g of cobalt acetate to 5ml of water and stir to dissolve, add 15ml of ammonia water containing 30% ammonia during stirring, add 0.7g of potassium hydroxide, 8.5g of ammonium molybdate, and 4.1g of nickel nitrate while stirring, and stir After dissolving, it was impregnated on 30g carrier, aged for 12 hours, dried at 120°C, and calcined at 500°C for 4 hours to obtain catalyst E.
Embodiment 3
[0042] Add 300g of alumina powder prepared by nitric acid method, add 18ml of auxiliary silica sol, 8.4ml of phosphoric acid, 3.8g of antimony nitrate, 1.8g of tin nitrate, add 140ml of water, knead and extrude, dry in the air at 100-120°C, 560 ℃ roasting for 6 hours, the prepared γ-Al containing silicon and phosphorus elements 2 o 3 carrier. At 50°C, add 6.4g of cobalt acetate to 5ml of water and stir to dissolve, add 15ml of ammonia water containing 30% ammonia while stirring, add 0.7g of potassium hydroxide, 0.4 of cesium hydroxide, 7.4g of ammonium molybdate, nitric acid 5.3 g of nickel was stirred and dissolved, impregnated on a 30 g carrier, aged for 12 hours, dried at 120° C., and calcined at 500° C. for 4 hours to obtain catalyst K.
PUM
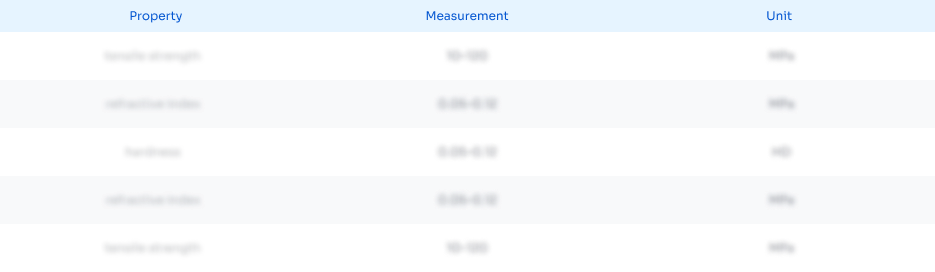
Abstract
Description
Claims
Application Information

- Generate Ideas
- Intellectual Property
- Life Sciences
- Materials
- Tech Scout
- Unparalleled Data Quality
- Higher Quality Content
- 60% Fewer Hallucinations
Browse by: Latest US Patents, China's latest patents, Technical Efficacy Thesaurus, Application Domain, Technology Topic, Popular Technical Reports.
© 2025 PatSnap. All rights reserved.Legal|Privacy policy|Modern Slavery Act Transparency Statement|Sitemap|About US| Contact US: help@patsnap.com