Non-oxide composite low-carbon magnesia-carbon brick
A non-oxide, carbon-magnesia-carbon brick technology, applied in the field of refractory materials, can solve the problems of low life, affecting the quality of special steel, easy peeling, etc., and achieve the effect of maintaining performance
- Summary
- Abstract
- Description
- Claims
- Application Information
AI Technical Summary
Problems solved by technology
Method used
Examples
Embodiment 1
[0016] Contains magnesia (5-0mm) 78.5%, graphite (400 mesh) 5%, magnesium aron (200 mesh) 4%, aluminum nitride (320 mesh) 4%, phenolic resin 3.5%, antioxidant: metal silicon ( 320 mesh) 1.5%, metal aluminum (320 mesh) 1.5%, silicon carbide (320 mesh) 2%.
[0017] Put magnesium aron, aluminum nitride, metal silicon, metal aluminum, silicon carbide, and magnesia fine powder into a V-shaped mixer in advance, mix for 10 minutes, and pack them into bags for later use; add magnesia particles, Mix phenolic resin for 3 minutes → add graphite and mix for 5 minutes → add pre-mixed fine powder and mix for 20 minutes, then pack into bags → weigh the mixed material and pour it into a 1000-ton friction press brick mold → press 10 times → finish Bricks are baked in a tunnel kiln at 200°C for 24 hours → packed out of the kiln.
Embodiment 2
[0019] It contains 94% of magnesia (5-0mm), 2% of graphite (400 mesh), 1.5% of sialon (320 mesh), and 2.5% of phenolic resin.
[0020] Put graphite, sialon, and magnesia fine powder into the V-type mixer in advance, mix for 10 minutes, and pack it into a bag for later use; add magnesia particles and phenolic resin to the 750-wheel mill and mix for 2 minutes → add pre-mixed fine powder and mix Pack in bags after 20 minutes → weigh the mixed material and pour it into a 1000-ton friction press brick mold → press 10 times → put the laid bricks in a tunnel kiln at 200°C for 24 hours → pack out of the kiln.
Embodiment 3
[0022] Contains magnesia (5-0mm) 75%, carbon black (N660) 1%, magnesium aron (200 mesh) 13%, silicon nitride (320 mesh) 5%, aluminum nitride (320 mesh) 2%, asphalt 4%.
[0023] Put magnesium aron, aluminum nitride, silicon nitride, carbon black, and magnesia fine powder into a conical double-helix mixer in advance, mix for 20 minutes, and pack it into a bag for later use; heat the asphalt to 180°C to become a liquid and keep it warm; Heat the magnesia granules to 200°C and put them into a 750 wheel mill and mix for 1 minute → add liquid asphalt and mix for 3 minutes → add pre-mixed fine powder and mix for 18 minutes → put it in an incubator → weigh the hot material and pour it in 600-ton friction press in the brick mold → press 8 times → pack the bricks after cooling.
PUM
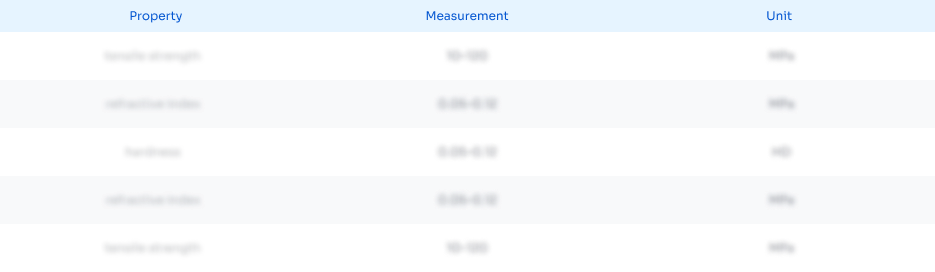
Abstract
Description
Claims
Application Information

- R&D
- Intellectual Property
- Life Sciences
- Materials
- Tech Scout
- Unparalleled Data Quality
- Higher Quality Content
- 60% Fewer Hallucinations
Browse by: Latest US Patents, China's latest patents, Technical Efficacy Thesaurus, Application Domain, Technology Topic, Popular Technical Reports.
© 2025 PatSnap. All rights reserved.Legal|Privacy policy|Modern Slavery Act Transparency Statement|Sitemap|About US| Contact US: help@patsnap.com