Preparation method of high porosity metal porous carrier materials
A carrier material, metal porous technology, applied in the direction of coating, etc., can solve the problems of low porosity of porous materials, difficult to maintain the shape of the material, collapse, etc., to achieve the effect of improving porosity and through porosity, and good performance.
- Summary
- Abstract
- Description
- Claims
- Application Information
AI Technical Summary
Problems solved by technology
Method used
Examples
Embodiment 1
[0014] The total amount of pore-forming agent added is 5wt%, wherein carboxymethyl cellulose (CMC) and urea CO (NH 2 ) 2 The ratio is 1:3, uniformly mixed with metal nickel powder with a particle size of less than 75 μm, mechanically pressed, and sintered under vacuum. The final sintering temperature is 900 ° C, and the holding time is 3.5 hours to obtain 1# sample.
Embodiment 2
[0016] The total amount of pore-forming agent added is 10wt%, wherein carboxymethyl cellulose (CMC) and urea CO (NH 2 ) 2 The ratio is 1:5, uniformly mixed with metal nickel powder with a particle size of less than 75 μm, mechanically pressed and molded, and sintered in a hydrogen atmosphere. After 3.5 hours, 2# sample was obtained.
Embodiment 3
[0018] The total amount of pore-forming agent added is 10wt%, wherein carboxymethyl cellulose (CMC) and urea CO (NH 2 ) 2 The ratio is 1:15, uniformly mixed with metal nickel powder with a particle size of less than 45 μm, mechanically pressed and molded, sintered in a hydrogen atmosphere, the low temperature holding temperature is 150 ° C ~ 250 ° C, the final sintering temperature is 880 ° C, and the holding time is 2.5 Hour, get 3# sample.
PUM
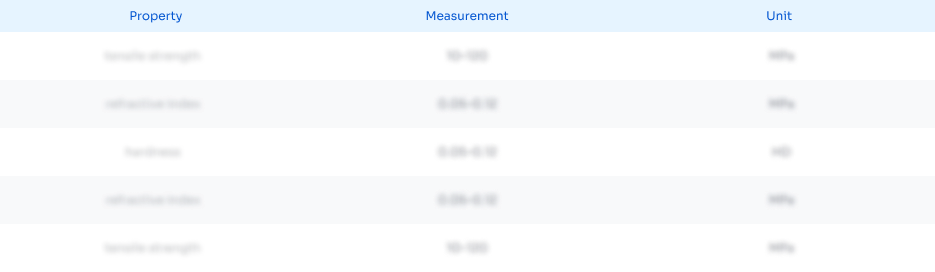
Abstract
Description
Claims
Application Information

- R&D
- Intellectual Property
- Life Sciences
- Materials
- Tech Scout
- Unparalleled Data Quality
- Higher Quality Content
- 60% Fewer Hallucinations
Browse by: Latest US Patents, China's latest patents, Technical Efficacy Thesaurus, Application Domain, Technology Topic, Popular Technical Reports.
© 2025 PatSnap. All rights reserved.Legal|Privacy policy|Modern Slavery Act Transparency Statement|Sitemap|About US| Contact US: help@patsnap.com