Process for vacuum pressure casting copper parts
A vacuum pressure casting and process technology, which is applied in the field of copper vacuum pressure casting technology, can solve the problems of long contact time, large copper shrinkage rate, and inability to improve the yield, and achieve high molding precision, long high temperature time, and high casting quality. Good results
- Summary
- Abstract
- Description
- Claims
- Application Information
AI Technical Summary
Problems solved by technology
Method used
Examples
Embodiment Construction
[0007] The details and process flow of the present invention will be described in detail below. This copper vacuum pressure casting process puts pure copper or copper alloy into the furnace. Since the casting temperature of pure copper and each copper alloy formula is different, the temperature to be adjusted is different. Generally, after the casting temperature reaches 950°C-1250°C, the furnace body is sealed immediately, and then filled with nitrogen. The upper part of the furnace body is provided with a vent hole outlet, which sinks due to the high density of nitrogen gas, while the oxygen gas with low density is blown by nitrogen gas. Press and float, and finally the aerobic gas in the furnace is discharged from the exhaust hole, so that the furnace is in an oxygen-free state. When the copper material is melted to a castable liquid state, the furnace body is pressurized so that the copper liquid overflows to the vacuum conveying pipeline. Since the temperature of the conv...
PUM
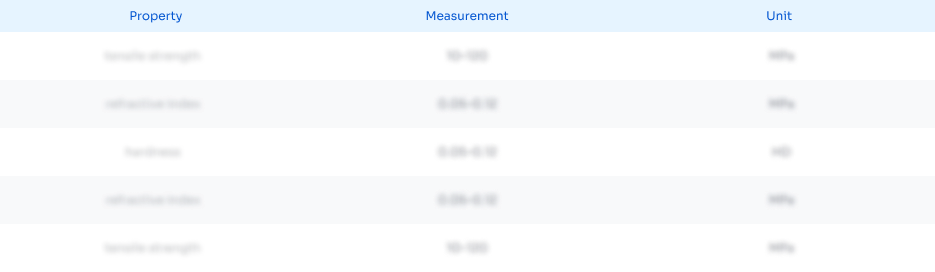
Abstract
Description
Claims
Application Information

- R&D
- Intellectual Property
- Life Sciences
- Materials
- Tech Scout
- Unparalleled Data Quality
- Higher Quality Content
- 60% Fewer Hallucinations
Browse by: Latest US Patents, China's latest patents, Technical Efficacy Thesaurus, Application Domain, Technology Topic, Popular Technical Reports.
© 2025 PatSnap. All rights reserved.Legal|Privacy policy|Modern Slavery Act Transparency Statement|Sitemap|About US| Contact US: help@patsnap.com