Testing apparatus for automatically measuring marine structure anchoring system stiffness
A technology for marine structures and mooring systems, which is applied in the field of automatic measurement and test devices for the stiffness of marine structure mooring systems, can solve problems such as process interruption, increased errors, troubles, etc., achieve good scientificity and accuracy, and be easy to implement. The effect of simple structure
- Summary
- Abstract
- Description
- Claims
- Application Information
AI Technical Summary
Problems solved by technology
Method used
Image
Examples
Embodiment Construction
[0016] The embodiments of the present invention are described in detail below in conjunction with the accompanying drawings: this embodiment is implemented on the premise of the technical solution of the present invention, and detailed implementation methods and specific operating procedures are provided, but the protection scope of the present invention is not limited to the following the described embodiment.
[0017] This embodiment includes: a model motion control component, a model connection component and a turntable. The model motion control component is connected with the upper turntable 6 through four support pipes 8 , and the model motion control component is connected with the lower model connection component through a threaded straight pipe 15 .
[0018] Such as figure 1 As shown, it represents the model motion control components and turntable, in which: two convex steel plates 1, two straight round tubes 2, two parallel angle steels 3, lead screw 4, servo motor 5...
PUM
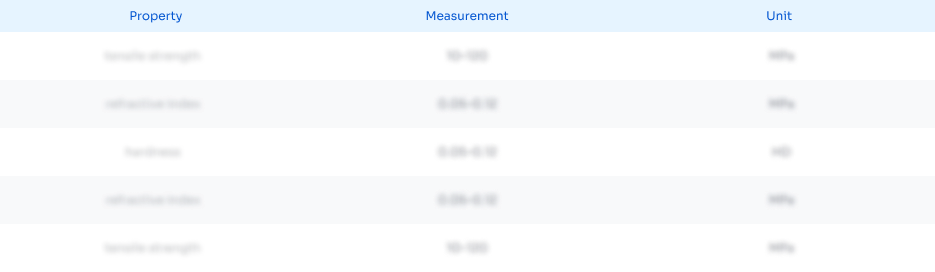
Abstract
Description
Claims
Application Information

- R&D Engineer
- R&D Manager
- IP Professional
- Industry Leading Data Capabilities
- Powerful AI technology
- Patent DNA Extraction
Browse by: Latest US Patents, China's latest patents, Technical Efficacy Thesaurus, Application Domain, Technology Topic, Popular Technical Reports.
© 2024 PatSnap. All rights reserved.Legal|Privacy policy|Modern Slavery Act Transparency Statement|Sitemap|About US| Contact US: help@patsnap.com