Self-temperature limiting heating belt and producing method thereof
A manufacturing method and heating belt technology, which are applied in the direction of ohmic resistance heating, heating element materials, electric heating devices, etc., can solve the problems of large equipment investment, high production conditions and costs, high equipment conditions, etc., and achieve high cross-linking degree, Low production conditions and the effect of reducing production costs
- Summary
- Abstract
- Description
- Claims
- Application Information
AI Technical Summary
Problems solved by technology
Method used
Image
Examples
Embodiment 1
[0020] Example 1 : 1. Raise the temperature of the rubber mixing machine to 85-90 ℃, and keep the temperature constant for 30-45 minutes, and mix various raw materials according to the following weight ratio: 100 parts of polyethylene, 40-45 parts of fluororubber, 55-65 parts of carbon black, Put 8-12 parts of joint agent and 0.5-1 part of antioxidant into the rubber mixing machine for mixing. The mixing time is 30 minutes. The temperature is controlled at 85-90°C for the first 15 minutes and 90-98 ℃, crush the PTC material after mixing, stir evenly, and then pack it for use;
[0021] 2. Preheat the single-screw extruder, keep the head temperature at 130°C, the body temperature at 126°C, the tail temperature at 102°C, and the mold temperature at 132°C; load the PTC material for packaging from the hopper at the tail end, and use Two regular stranded wire cores of 7 tinned round copper wires at equal intervals, each round copper wire φ = 0.49 mm, pass through the extrusion die...
PUM
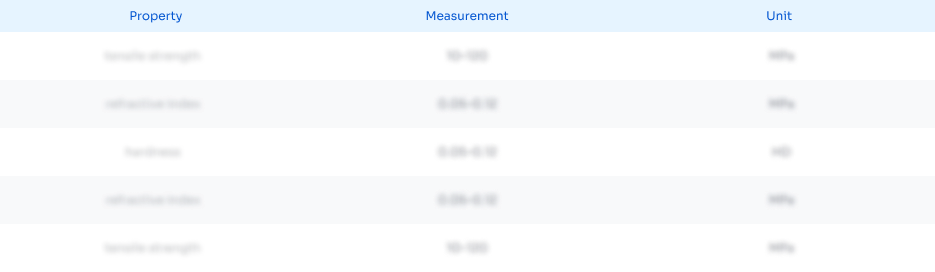
Abstract
Description
Claims
Application Information

- R&D
- Intellectual Property
- Life Sciences
- Materials
- Tech Scout
- Unparalleled Data Quality
- Higher Quality Content
- 60% Fewer Hallucinations
Browse by: Latest US Patents, China's latest patents, Technical Efficacy Thesaurus, Application Domain, Technology Topic, Popular Technical Reports.
© 2025 PatSnap. All rights reserved.Legal|Privacy policy|Modern Slavery Act Transparency Statement|Sitemap|About US| Contact US: help@patsnap.com