Welding agent and manufacturing process thereof
A technology of welding flux and particles, applied in the direction of welding medium, manufacturing tools, welding equipment, etc., can solve the problems of joint tensile strength drop, shorten the service life of joints, reduce the strength of joints, etc., to increase brightness and smoothness, avoid Cellular phenomenon, the effect of reducing the generation of gas
- Summary
- Abstract
- Description
- Claims
- Application Information
AI Technical Summary
Problems solved by technology
Method used
Examples
Embodiment 1
[0019] Embodiment one, its basic composition is as follows:
[0020] 15% copper powder oxidized to copper oxide, particles in 20-100 mesh: 100 grams
[0021] Aluminum powder: 5 grams, particles in 80 mesh;
[0022] Calcium fluoride: 0.1 g;
[0023] Silicon dioxide: 0.1 g;
[0024] Calcium metasilicate: 1 g:
[0025] Graphite powder: 0.1 g:
[0026] Silver powder: 1 g.
[0027] The method for making the solder is as follows according to the formula: bake copper oxide, calcium fluoride, silicon dioxide, metasilicate and carbon at a temperature of 40°C for 30 minutes respectively, and then bake copper oxide, calcium fluoride, Aluminum powder, calcium fluoride, metasilicate, carbon and silver powder are mixed together, stirred until uniform, and then packaged to be a finished product. The aluminum and silver powder are in a dry state when mixed.
Embodiment 2
[0028] Embodiment two, its basic composition is as follows:
[0029] 25% copper powder oxidized to copper oxide, particles in 20-100 mesh: 100 grams
[0030] Aluminum powder: 15 grams, particles in 100 mesh;
[0031] Calcium fluoride: 1 g;
[0032] Silicon dioxide: 1 g;
[0033] Calcium metasilicate: 3 grams:
[0034] Graphite powder: 0.5 grams;
[0035] Silver powder: 1 gram;
[0036] The method for making the solder is as follows according to the formula: bake copper oxide, calcium fluoride, silicon dioxide, metasilicate and carbon at a temperature of 40°C for 30 minutes respectively, and then bake copper oxide, calcium fluoride, Aluminum powder, calcium fluoride, metasilicate, carbon and silver powder are mixed together, stirred until uniform, and then packaged to be a finished product. The aluminum and silver powder are in a dry state when mixed.
Embodiment 3
[0037] Embodiment three, its basic composition is as follows:
[0038] Copper powder 40% oxidized to copper oxide, particles in 20-100 mesh: 100 grams
[0039] Aluminum powder: 30 grams, particles in 120 mesh;
[0040] Calcium fluoride: 3 grams;
[0041] Silicon dioxide: 4 grams;
[0042] Calcium metasilicate: 3 grams:
[0043] Graphite powder: 1 gram:
[0044] Silver powder: 3 grams.
[0045] The method for making the solder is as follows according to the formula: bake copper oxide, calcium fluoride, silicon dioxide, metasilicate and carbon at a temperature of 40°C for 30 minutes respectively, and then bake copper oxide, calcium fluoride, Aluminum powder, calcium fluoride, metasilicate, carbon and silver powder are mixed together, stirred until uniform, and then packaged to be a finished product. The aluminum and silver powder are in a dry state when mixed.
PUM
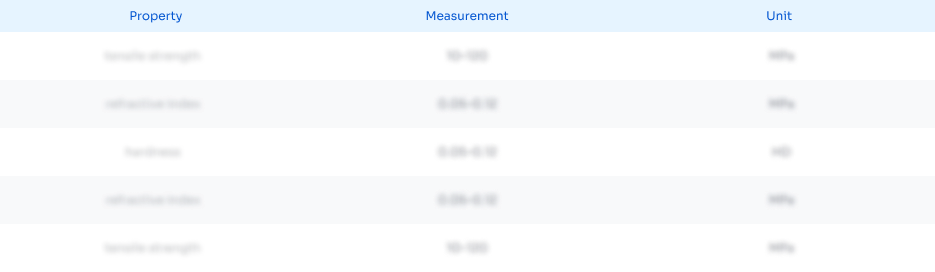
Abstract
Description
Claims
Application Information

- R&D Engineer
- R&D Manager
- IP Professional
- Industry Leading Data Capabilities
- Powerful AI technology
- Patent DNA Extraction
Browse by: Latest US Patents, China's latest patents, Technical Efficacy Thesaurus, Application Domain, Technology Topic, Popular Technical Reports.
© 2024 PatSnap. All rights reserved.Legal|Privacy policy|Modern Slavery Act Transparency Statement|Sitemap|About US| Contact US: help@patsnap.com