Process for removing mixed crystal defect of large rotor forging
A forging and process technology, which is applied in the field of eliminating mixed crystal defects in low-pressure rotor forgings of large steam turbines, and can solve problems such as increased pressure and normalizing times, abnormal grain growth, and mixed crystals
- Summary
- Abstract
- Description
- Claims
- Application Information
AI Technical Summary
Problems solved by technology
Method used
Examples
Embodiment Construction
[0004] For 300,000-kilowatt steam turbine low-pressure rotor forgings, the maximum diameter of the finished product is 1950mm. In order to control the temperature of the core of the forging within a reasonable temperature range for each forming fire, after the compaction fire is completed, the rotor forging is air-cooled for 4 to 4.5 hours, and then returned to the furnace for heating: the heating temperature is 1200-1270 ℃, the heating time is 10-12 hours. After that, take it out of the furnace and forge for 2 hours, air cool for 1 hour, and then return to the furnace for heating: the heating furnace temperature is 1200-1270 degrees, and the heating time is 8-10 hours. After that, it is forged out of the furnace and sent to heat treatment after completion.
[0005] During the forming process, the temperature of the core of the rotor forging is controlled below 1120 degrees, because experiments have shown that when the temperature is higher than 1150 degrees, the materials 30...
PUM
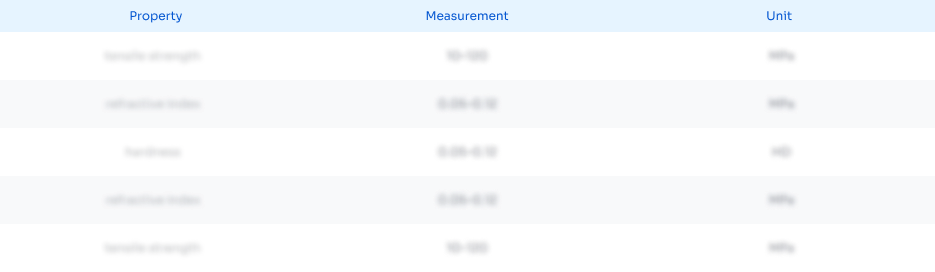
Abstract
Description
Claims
Application Information

- R&D Engineer
- R&D Manager
- IP Professional
- Industry Leading Data Capabilities
- Powerful AI technology
- Patent DNA Extraction
Browse by: Latest US Patents, China's latest patents, Technical Efficacy Thesaurus, Application Domain, Technology Topic, Popular Technical Reports.
© 2024 PatSnap. All rights reserved.Legal|Privacy policy|Modern Slavery Act Transparency Statement|Sitemap|About US| Contact US: help@patsnap.com