Vehicle dampener
A technology for shock absorbers and vehicles, which is applied in the direction of shock absorbers, springs/shock absorbers, shock absorbers, etc., and can solve the problems of small variation range of shock absorption and damping, fast shock absorption speed, and slow shock absorption speed. To achieve a wide range of shock absorption and damping effects, improve the mutual loss angle of the overall stiffness, and improve the effect of shock absorption and buffering capacity
- Summary
- Abstract
- Description
- Claims
- Application Information
AI Technical Summary
Problems solved by technology
Method used
Image
Examples
Embodiment Construction
[0024] The present invention will be described in further detail below in conjunction with accompanying drawing embodiment:
[0025] Such as Figure 1 ~ Figure 1 0 shows a preferred embodiment of the present invention. Such as Figure 1 ~ Figure 1 As shown in 0, the vehicle shock absorber in this embodiment has an inner cylinder body 1 made of metal, an outer cylinder body 2 made of metal surrounding the outer periphery of the inner cylinder body 1, and a gap between the inner cylinder body 1 and the outer cylinder body 2. The elastic body 3 made of rubber material in between, the elastic body 3 has an inner cylinder 31 adapted to the outer circumference of the inner cylinder body 1, an outer cylinder adapted to the inner side of the outer cylinder body 2, the upper outer cylinder 32 and the lower outer cylinder separated by the middle. An outer cylinder 33 is formed, an upper connecting portion 34 is integrally formed between the upper outer cylinder 32 and the inner cylind...
PUM
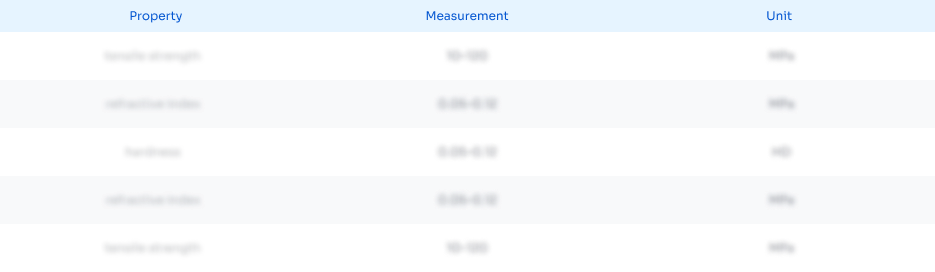
Abstract
Description
Claims
Application Information

- R&D
- Intellectual Property
- Life Sciences
- Materials
- Tech Scout
- Unparalleled Data Quality
- Higher Quality Content
- 60% Fewer Hallucinations
Browse by: Latest US Patents, China's latest patents, Technical Efficacy Thesaurus, Application Domain, Technology Topic, Popular Technical Reports.
© 2025 PatSnap. All rights reserved.Legal|Privacy policy|Modern Slavery Act Transparency Statement|Sitemap|About US| Contact US: help@patsnap.com