Preparation process of poly-1,8-naphthalenediamine
A naphthalene diamine and chemical oxidation technology, applied in 1 field, can solve problems such as production area constraints and inability to obtain a large amount of polymers, and achieve high production rate and large production scale
- Summary
- Abstract
- Description
- Claims
- Application Information
AI Technical Summary
Problems solved by technology
Method used
Image
Examples
Embodiment 1
[0014] Accurately weigh 0.791 g (5 mmol) of 1,8-naphthalene diamine and dissolve it in 50 mL of acetonitrile, and ultrasonicate for 3 to 5 minutes to promote its full dissolution. Weigh 1.141 g (5 mmol) of ammonium persulfate according to the oxidant monomer ratio of 1:1, dissolve it in 50 mL of distilled water, and place it in a constant temperature water bath at 20° C. to preheat to the reaction temperature. The oxidant solution at 20°C is added dropwise to the monomer solution at a rate of about 1 drop / 3s. After the dropwise addition, the reaction was continued for 6h. After the reaction is finished, filter, and wash the initial product with distilled water until the filtrate is colorless, then transfer the polymer filter cake to a beaker and continue to stir and wash overnight, and obtain a soft black powdery polymer after suction drying, with a yield of 0.672g and a yield of 85.0%.
Embodiment 2
[0016] Accurately weigh 0.791 g (5 mmol) of 1,8-naphthalene diamine and dissolve it in 50 mL of acetonitrile, and ultrasonicate for 3 to 5 minutes to promote its full dissolution. Weigh 0.5705g (2.5mmol) ammonium persulfate according to the oxidant monomer ratio of 0.5:1 and dissolve it in 50mL of distilled water, and place it in a constant temperature water bath at 20°C to preheat to the reaction temperature. The 20°C oxidant solution was added dropwise to the monomer solution. After the dropwise addition, the reaction was continued for 6h. After the reaction is finished, filter, and wash the initial product with distilled water until the filtrate is colorless, then transfer the polymer filter cake to a beaker and continue to stir and wash overnight, and obtain a soft black powdery polymer after suction drying, with a yield of 0.245g and a yield of 31.0%.
Embodiment 3
[0018] Accurately weigh 0.791 g (5 mmol) of 1,8-naphthalene diamine and dissolve it in 50 mL of acetonitrile, and ultrasonicate for 3 to 5 minutes to promote its full dissolution. Weigh 2.282g (10mmol) of ammonium persulfate according to the oxidant monomer ratio of 2:1, dissolve it in 50mL of distilled water, and place it in a constant temperature water bath at 20°C to preheat to the reaction temperature. The 20°C oxidant solution was added dropwise to the monomer solution. After the dropwise addition, the reaction was continued for 6h. After the reaction is finished, filter, and wash the initial product with distilled water until the filtrate is colorless, then transfer the polymer filter cake to a beaker and continue stirring and washing overnight, and obtain a soft black powdery polymer after suction drying, with a yield of 0.775g and a yield of 98.0%.
PUM
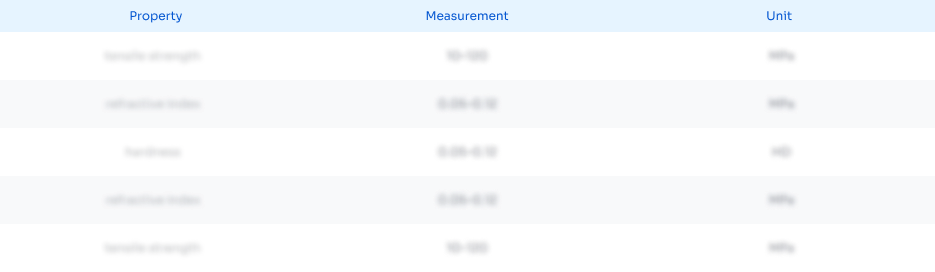
Abstract
Description
Claims
Application Information

- R&D
- Intellectual Property
- Life Sciences
- Materials
- Tech Scout
- Unparalleled Data Quality
- Higher Quality Content
- 60% Fewer Hallucinations
Browse by: Latest US Patents, China's latest patents, Technical Efficacy Thesaurus, Application Domain, Technology Topic, Popular Technical Reports.
© 2025 PatSnap. All rights reserved.Legal|Privacy policy|Modern Slavery Act Transparency Statement|Sitemap|About US| Contact US: help@patsnap.com