Process for preparing compound of cyclohexdiol
A manufacturing method and technology of cyclohexanediol, applied in hydrogenation preparation, organic chemistry and other directions, can solve the problems of high cost, high temperature and high pressure hydrogenation reaction of refractory phenol, high price, etc. The effect of deep processing and utilization, reducing production cost
- Summary
- Abstract
- Description
- Claims
- Application Information
AI Technical Summary
Problems solved by technology
Method used
Examples
Embodiment 1
[0014] Embodiment 1: in the three-necked flask of 500 milliliters, install thermometer, stirrer, add hydroquinone (10 millimoles, 1.11 grams), Ni-Al alloy (10g), water (100 milliliters), then start stirring and heating to 90°C. A 1% aqueous sodium hydroxide solution (100 ml) was added dropwise over 1 hour. Control the reaction temperature to be 90°C-100°C. After the dropwise addition of the 1% aqueous sodium hydroxide solution was completed, stirring was continued at this temperature for 5 hours. Then it was cooled to room temperature, filtered, and the insoluble matter was removed by filtration, the aqueous solution was extracted with ethyl acetate, the organic layer was dried with anhydrous magnesium sulfate, and then concentrated under reduced pressure. Then the concentrated product was analyzed by gas chromatography, the conversion rate of hydroquinone was 100%, and the yield rate of 1,4-cyclohexanediol was 84%.
Embodiment 2
[0015] Embodiment 2: in the three-necked flask of 500 milliliters, install thermometer, stirrer, add hydroquinone (10 millimoles, 1.11 grams), Ni-Al alloy (7g), water (100 milliliters), then start stirring and heating to 80°C. A 3% aqueous sodium hydroxide solution (100 ml) was added dropwise over 1 hour. The reaction temperature is controlled to be 80°C-100°C. After the dropwise addition of the 3% aqueous sodium hydroxide solution was completed, stirring was continued at this temperature for 7 hours. Then it was cooled to room temperature, filtered, and the insoluble matter was removed by filtration, the aqueous solution was extracted with ethyl acetate, the organic layer was dried with anhydrous magnesium sulfate, and then concentrated under reduced pressure. Then the concentrated product was analyzed by gas chromatography, the conversion rate of hydroquinone was 100%, and the yield rate of 1,4-cyclohexanediol was 83%.
Embodiment 3
[0016] Embodiment 3: in the three-necked bottle of 500 milliliters, install thermometer, stirrer, add hydroquinone (10 millimoles, 1.11 grams), Ni-Al alloy (8g), water (100 milliliters), then start stirring and heating to 90°C. 8% cesium hydroxide aqueous solution (100 ml) was added dropwise over 1.5 hours. Control the reaction temperature to be 90°C-100°C. After the dropwise addition of the 8% cesium hydroxide aqueous solution was completed, stirring was continued at this temperature for 5 hours. Then it was cooled to room temperature, filtered, and the insoluble matter was removed by filtration, the aqueous solution was extracted with ethyl acetate, the organic layer was dried with anhydrous magnesium sulfate, and then concentrated under reduced pressure. Then the concentrated product was analyzed by gas chromatography, the conversion rate of hydroquinone was 100%, and the yield rate of 1,4-cyclohexanediol was 82%.
PUM
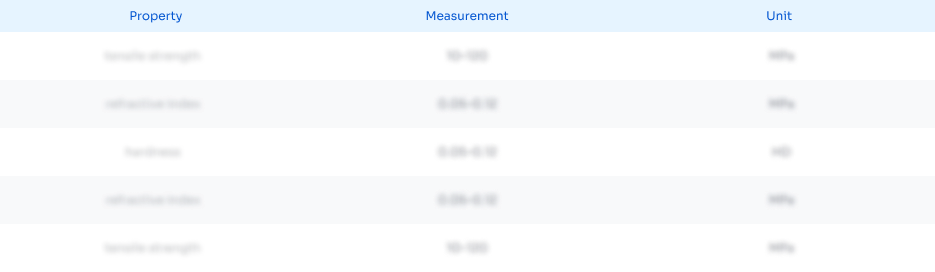
Abstract
Description
Claims
Application Information

- R&D
- Intellectual Property
- Life Sciences
- Materials
- Tech Scout
- Unparalleled Data Quality
- Higher Quality Content
- 60% Fewer Hallucinations
Browse by: Latest US Patents, China's latest patents, Technical Efficacy Thesaurus, Application Domain, Technology Topic, Popular Technical Reports.
© 2025 PatSnap. All rights reserved.Legal|Privacy policy|Modern Slavery Act Transparency Statement|Sitemap|About US| Contact US: help@patsnap.com