In situ getter pump system and method
A technology for processing wafers and on-site pumps, applied to pumps, electrical components, liquid variable capacity machinery, etc., can solve the problems of increased process costs, frequent regeneration, high argon price, etc., reduce transition time, increase productivity and profit Efficiency and reduced downtime
- Summary
- Abstract
- Description
- Claims
- Application Information
AI Technical Summary
Problems solved by technology
Method used
Image
Examples
Embodiment Construction
[0040] The wafer processing system 10 of FIG. 1 includes a first housing 12 enclosing a remote wafer robot 14 and a second housing 16 defining a processing chamber 18 . The system 10 also includes a mechanical pump 20, a cryopump 22, a gas delivery system 24, a plasma generator 26 for generating a plasma, and a microprocessor-based controller 28 for controlling the many operations of the wafer processing system 10 . The present invention also includes an in situ getter system pump 30 comprising a getter miniature assembly 32, a baffle 33, a controllable power supply 34, a residual gas analyzer (RGA) 36 and a microprocessor based The controller 38. The wafer processing system 10 processes a semiconductor wafer 40 placed in a processing chamber 18 using a remote-controlled wafer robot 14 .
[0041] The fabrication details of the first housing 12 and the manipulator 14 for remote control of the wafer are well known to those skilled in the art. Housing 12 defines a manipulator ...
PUM
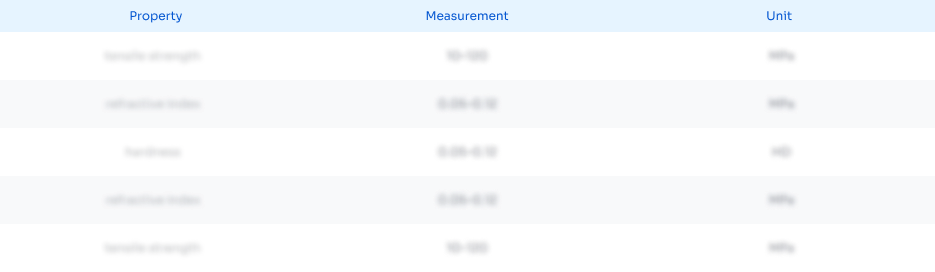
Abstract
Description
Claims
Application Information

- R&D
- Intellectual Property
- Life Sciences
- Materials
- Tech Scout
- Unparalleled Data Quality
- Higher Quality Content
- 60% Fewer Hallucinations
Browse by: Latest US Patents, China's latest patents, Technical Efficacy Thesaurus, Application Domain, Technology Topic, Popular Technical Reports.
© 2025 PatSnap. All rights reserved.Legal|Privacy policy|Modern Slavery Act Transparency Statement|Sitemap|About US| Contact US: help@patsnap.com