Method for forming partitions of plasma display panel by using sandblasting process
a technology of plasma display panel and sandblasting process, which is applied in the manufacture of electrode systems, cold cathode manufacturing, and electric discharge tube/lamp manufacture, etc. it can solve the problems of mask exfoliation, slight operation sound (buzz sound), etc., and achieve the effect of enhancing the protection of sub-partitions in the cutting process, reducing stress concentration, and reducing the depth of side cuts
- Summary
- Abstract
- Description
- Claims
- Application Information
AI Technical Summary
Benefits of technology
Problems solved by technology
Method used
Image
Examples
first embodiment
(First Embodiment)
[0031]FIG. 2 is a plan view showing a mask pattern of a first embodiment. A partition pattern of the PDP of the first embodiment is a stripe pattern. The partition is formed basically in the same manner as the conventional process explained with reference to FIG. 12, which includes patterning a sheet-like partition material 2 that covers the entire surface of a glass substrate 1 that is a panel material by using a sandblasting process, and then baking the partition material 2. The difference from the conventional process is that a mask 30 used for patterning extends over a display area 10 and a non-display area 11 at both sides of the display area 10. The display area 10 means an area in which cells are formed on the glass substrate 1, and it corresponds to a display screen of a completed PDP. As to formation of the partition material, 2 there are some methods similarly to the conventional process, i.e., a method of applying low melting point glass paste to the gla...
second embodiment
(Second Embodiment)
[0036]FIG. 4 is a plan view showing a mask pattern of a second embodiment. FIG. 5 is a diagram showing an enlarged part of the mask pattern of the second embodiment. In the PDP of the second embodiment, the partition pattern is also a stripe pattern. The partition is formed in the same way as the first embodiment, which includes patterning a sheet-like partition material 2b that covers the entire surface of a glass substrate 1b by using a sandblasting process and a mask 30b that is a unit of a main mask 3b and a sub mask 4b, and then baking the partition material 2b. The second embodiment has three characteristics as follows.
[0037](1) At the same time as forming the mask 30b, auxiliary masks 5 are formed at both sides of the mask 30b and separated from the mask 30b.
[0038](2) Among bands that constitute the pattern of the sub mask 4b and are formed in the direction perpendicular to the stripe partition, the most outside band is thicker than bands constituting the p...
third embodiment
(Third Embodiment)
[0050]FIG. 11 is a plan view showing a mask pattern of a third embodiment. The third embodiment is applied to a multiple making process in which partitions for a plurality of PDPs are formed on one substrate simultaneously, and then the substrate is divided. The example shown in FIG. 11 shows an example in which partitions for three PDPs are formed simultaneously, and each of the three display areas 10a, 10b and 10c in FIG. 11 corresponds to a partition portion of one PDP. The partition pattern of the PDP of the third embodiment is also a stripe pattern. The partition is formed by the process in the same way as the first embodiment, which includes patterning a sheet-like partition material 2c that covers the entire surface of a glass substrate 1c by using a sandblasting process and a mask 30b that is a unit of a main mask and a sub mask, and then baking the partition material 2c. The glass substrate 1c has a size of 1460 mm×1050 mm for manufacturing a 32-inch PDP.
[...
PUM
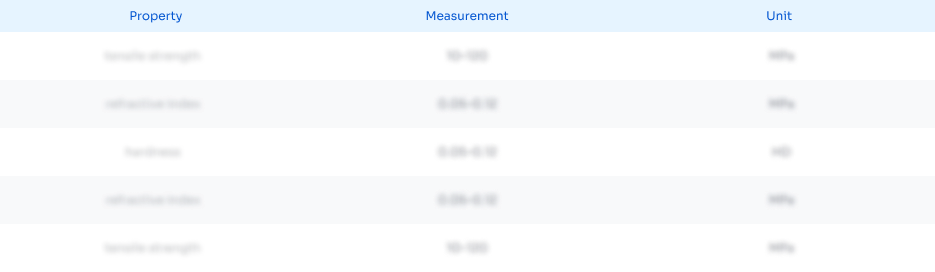
Abstract
Description
Claims
Application Information

- R&D
- Intellectual Property
- Life Sciences
- Materials
- Tech Scout
- Unparalleled Data Quality
- Higher Quality Content
- 60% Fewer Hallucinations
Browse by: Latest US Patents, China's latest patents, Technical Efficacy Thesaurus, Application Domain, Technology Topic, Popular Technical Reports.
© 2025 PatSnap. All rights reserved.Legal|Privacy policy|Modern Slavery Act Transparency Statement|Sitemap|About US| Contact US: help@patsnap.com