Vibration damping system
a technology of vibration damping and damping body, which is applied in the direction of shock absorbers, machine supports, other domestic objects, etc., can solve the problems of weak tensile force in the laminating direction and vibration damping system of the type, so as to prolong the service life and improve the fatigue strength of the laminated body
- Summary
- Abstract
- Description
- Claims
- Application Information
AI Technical Summary
Benefits of technology
Problems solved by technology
Method used
Image
Examples
first embodiment
[0049]As shown in FIG. 1(B), hard plates 4 having rigidity and soft members 4 having viscoelasticity are alternately laminated to form a laminated body 3, and upper and lower shoe members 1, 2 are arranged on both end portions of the laminated body 3 to form the vibration damping body 6. The hard plates 4 may be comprised of a suitable metal material, such as iron, aluminum or the like. Besides a metal material, the hard plates 4 may be comprised of a resin material, such as nylon, and adhered to the soft members is the case with the metal material.
[0050]The soft members 5 having viscoelasticity are generally formed by molding various types of vulcanized rubber as the raw material. Such rubber material may include, for example, ethylene-propylene rubber (EPR, EPDM), nitrile rubber (NBR), butyl rubber, halogenated butyl rubber, chloroprene rubber (CR), natural rubber (NR), isoprene rubber (IR), styrene-butadiene rubber (SBR), butadiene rubber (BR), and a blend thereof. Alternatively,...
second embodiment
[0081]FIGS. 4(A) and 4(B) are a plan view and a longitudinal sectional view of the vibration damping system according to a modification of the above-described embodiment of the present invention, respectively. In this modified embodiment, each dividing location of the vibration damping body 6, i.e., each parting face 8 in the laminated body 3, is covered over the entire periphery and sealed from outside, by a cover member 21 that is made of a suitable material, such as rubber film body. The cover member 21 functions as a dust cover for preventing entry of foreign matters into a space surrounding the parting face 8. The cover member 21 may be comprised of a toroidal rubber film having a bellow shape with a single protrusion. It is further preferred that the cover member is brought into contact with the outer periphery of the vibration damping body 6, bridging across the parting faces 8, under its own resilient shrinkage force, from the viewpoint of achieving a sufficiently tight cont...
PUM
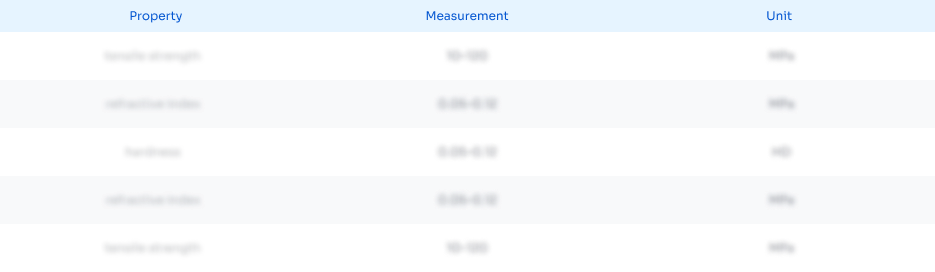
Abstract
Description
Claims
Application Information

- R&D
- Intellectual Property
- Life Sciences
- Materials
- Tech Scout
- Unparalleled Data Quality
- Higher Quality Content
- 60% Fewer Hallucinations
Browse by: Latest US Patents, China's latest patents, Technical Efficacy Thesaurus, Application Domain, Technology Topic, Popular Technical Reports.
© 2025 PatSnap. All rights reserved.Legal|Privacy policy|Modern Slavery Act Transparency Statement|Sitemap|About US| Contact US: help@patsnap.com