Optical package with double formed leadframe
a leadframe and optical package technology, applied in the field of optical package, can solve the problems of high cost, high cost of mold design and construction, and use of the top side of the die pad of the leadframe, and achieve the effects of low cost, easy and less expensive to make, and low cos
- Summary
- Abstract
- Description
- Claims
- Application Information
AI Technical Summary
Benefits of technology
Problems solved by technology
Method used
Image
Examples
Embodiment Construction
[0022]FIG. 1 is a cross-sectional diagram of an optical system in prior art. A leadframe including a substantially planar die pad 18 within and connected to the leadframe has multiple lead fingers 17 at specific bending angles, wherein a portion of the lead fingers is mounted on a top surface of a printed circuit board 16. There is an integrated circuit die 14 attached on the upward first pad surface of the leadframe. A top encapsulating dielectric material 13 is applied onto the upward first pad surface and a bottom encapsulating dielectric material 15 onto a downward second pad surface. The top encapsulating dielectric material 13 also embraces the integrated circuit die 14 and a portion of the multiple lead fingers 17. Generally, the encapsulating dielectric material 13 is transparent for a package embodied an optical integrated circuit die 14, wherein the optical integrated circuit die 14 receives the optical information 12 from environment outside, manipulates the variation of ...
PUM
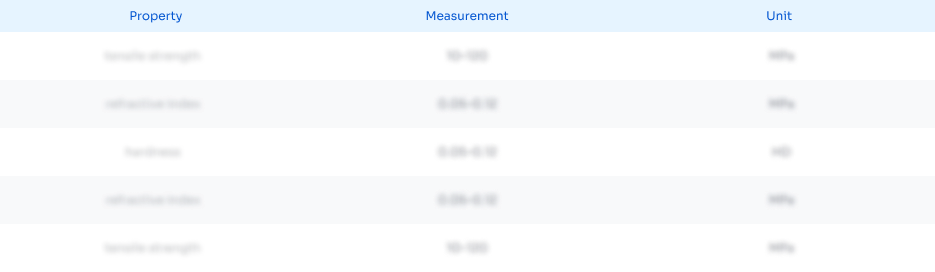
Abstract
Description
Claims
Application Information

- R&D
- Intellectual Property
- Life Sciences
- Materials
- Tech Scout
- Unparalleled Data Quality
- Higher Quality Content
- 60% Fewer Hallucinations
Browse by: Latest US Patents, China's latest patents, Technical Efficacy Thesaurus, Application Domain, Technology Topic, Popular Technical Reports.
© 2025 PatSnap. All rights reserved.Legal|Privacy policy|Modern Slavery Act Transparency Statement|Sitemap|About US| Contact US: help@patsnap.com