Fungible bitumen from paraffinic centrifugation
- Summary
- Abstract
- Description
- Claims
- Application Information
AI Technical Summary
Benefits of technology
Problems solved by technology
Method used
Image
Examples
example 1
[0059]Experiments were conducted to investigate the ability of a three-phase decanter centrifuge to separate a light phase product having a water content below about 2.0 wt % from naphthenic diluted froth. To mimic separation in a decanter centrifuge, a benchtop Hotspin™ centrifuge was run at particular speeds and spin times. Samples of naphthenic diluted froth contained bitumen (44 wt %), naphtha (26 wt %), water (22 wt %), and solids (8 wt %), with the N:B ratio being about 0.6. The samples were maintained at 80° C. and spun at 1500 rpm for 1, 2, 4, and 8 mins. Two samples were prepared for each spin time. The reported values are the average values between the two samples at each spin time.
[0060]Three distinguishable interfaces between light phase, heavy phase and solids were achieved in each sample after each centrifugation interval. The separated heavy phase became less turbid when spun longer, while the overall combined volume of heavy phase and solids remained relatively const...
example 2
[0064]An experiment was conducted to assess the feasibility of a three-phase decanter centrifuge to convey separated solids in a paraffinic diluted froth treatment process. Pentane (C5H12) and undiluted froth were mixed in diluent to bitumen (D / B) ratios of about 1.8, 2.8, 3.5, and 4.5 by weight. These samples were poured into 8 oz jars and cold spun (room temperature) for 20 minutes at about 2,000 RPM. After spinning in the centrifuge, the liquid phase was poured out leaving only the solids. FIGS. 5A-D show these solids at the various DIB ratios before and after kneading with a lab spoon to simulate conveyance in a decanter centrifuge. For comparison, kneaded naphthenic cake is shown in FIG. 6. For each solid, the relative cohesive property, adhesion to the beaker and lab spoon, and shear strength were inspected.
[0065]It was expected that separating paraffinic solids trapped in viscous medium might be challenging in a decanter centrifuge. However, it was observed that the paraffini...
example 3
[0066]Experiments were conducted to compare naphthenic treatment of bitumen froth at various solvent-to-bitumen ratios and paraffinic (octane) treatment of bitumen froth at various solvent-to-bitumen ratios using centrifugation. Each of the naphtha and octane solvents and bitumen froth were first heated inside a hot water bath at 80° C. To mimic separation in a decanter centrifuge, a benchtop Hotspin™ centrifuge was used. Two sets of experiments were performed for each of naphtha as solvent and octane as solvent. In Test 1 for naphtha, solvent-to-bitumen (S / B) ratios (wt / wt) of 0.5, 0.7, 1.0 and 2.0 were tested. In Test 1 for octane, solvent-to-bitumen (S / B) ratios (wt / wt) of 0.5, 1.0, 2.0 and 4.0 were tested. In Test 2 for naphtha, higher solvent-to-bitumen (S / B) ratios (wt / wt) of 2.0, 3.0, 3.5, 4.0, 4.5 and 5.5 were tested. In Test 2 for octane, solvent-to-bitumen (S / B) ratios (wt / wt) of 1.0, 1.2, 1.4, 1.5, 1.6, 1.8 and 2.0 and 4.0 were tested. Froth mixtures at each solvent ratio...
PUM
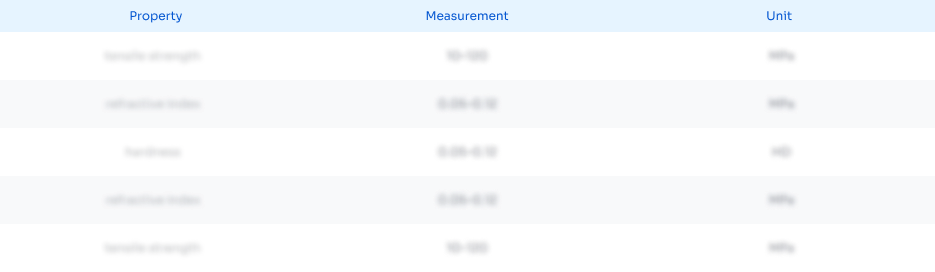
Abstract
Description
Claims
Application Information

- R&D
- Intellectual Property
- Life Sciences
- Materials
- Tech Scout
- Unparalleled Data Quality
- Higher Quality Content
- 60% Fewer Hallucinations
Browse by: Latest US Patents, China's latest patents, Technical Efficacy Thesaurus, Application Domain, Technology Topic, Popular Technical Reports.
© 2025 PatSnap. All rights reserved.Legal|Privacy policy|Modern Slavery Act Transparency Statement|Sitemap|About US| Contact US: help@patsnap.com