Method and system for model-based design and layout of an integrated circuit
a model-based design and integrated circuit technology, applied in the direction of cad circuit design, program control, instruments, etc., can solve the problems of many ic design failures, ic design manufacturing has gotten steadily more difficult, and feature dimensions vary, so as to achieve the effect of increasing the quantity of data, increasing the complexity of physical and lithographic effects during manufacture, and increasing the amount of resources
- Summary
- Abstract
- Description
- Claims
- Application Information
AI Technical Summary
Benefits of technology
Problems solved by technology
Method used
Image
Examples
Embodiment Construction
[0022]The present approach is directed to an improved method, system, and computer readable medium for performing routing, full chip flows, and “hotspot” detection. As used herein, the term “hotspot” refers to a portion of a design layout that is identified as corresponding to a manufacturing-related problem, such as may be caused by lithography, chemical metal polishing (CMP), etch, strain, critical area analysis, or any combination thereof. Some embodiments of the invention utilize pattern matching to detect hotspots and to provide lithographically aware routing and chip design, by creating and accessing a bad pattern library. The term “bad pattern”, according to some embodiments, refers to any layout shape or shape pattern that has a negative impact on yield or functionality due to, for example, lithography, CMP, strain, critical area analysis, and other manufacturing related issues. In this document, the term “hotspot” may be used in certain places synonymously with the term “ba...
PUM
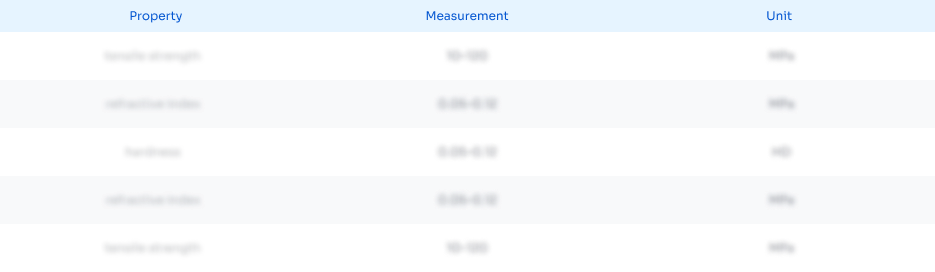
Abstract
Description
Claims
Application Information

- R&D
- Intellectual Property
- Life Sciences
- Materials
- Tech Scout
- Unparalleled Data Quality
- Higher Quality Content
- 60% Fewer Hallucinations
Browse by: Latest US Patents, China's latest patents, Technical Efficacy Thesaurus, Application Domain, Technology Topic, Popular Technical Reports.
© 2025 PatSnap. All rights reserved.Legal|Privacy policy|Modern Slavery Act Transparency Statement|Sitemap|About US| Contact US: help@patsnap.com