Heat exchanger and refrigerant cycle device using the same
a technology of heat exchanger and refrigerant cycle, which is applied in the direction of defrosting, domestic cooling apparatus, etc., can solve the problems of dispersion between the surface of the heat exchanging portion and the ice, and achieve the effect of reducing heat energy
- Summary
- Abstract
- Description
- Claims
- Application Information
AI Technical Summary
Benefits of technology
Problems solved by technology
Method used
Image
Examples
first embodiment
[0033]FIG. 1 is a schematic diagram showing a refrigerant cycle device according to a first embodiment of the invention. In the present embodiment, the refrigerant cycle device is typically used for a vehicle air conditioner 1 mounted to an electrical vehicle (EV) or a hybrid vehicle (HV), for example.
[0034]As shown in FIG. 1, the air conditioner 1 includes a vapor-compression refrigerant cycle 10 and an interior air conditioning unit 20. The refrigerant cycle 10 is configured to be switchable between a cooling operation mode and a heating operation mode.
[0035]The refrigerant cycle 10 includes a compressor 11, an interior heat exchanger 12, an exterior heat exchanger 13, a decompression device 14, a four-way valve 15 and a controller (ECU) 16.
[0036]The compressor 11 is disposed in an engine compartment to draw refrigerant, to compress the drawn refrigerant and to discharge the compressed refrigerant. For example, the compressor 11 is an electrical compressor in which a fixed-displac...
second embodiment
[0087]A second embodiment of the present invention will be described with reference to FIG. 8. FIG. 8 is a schematic perspective view showing thermal deformation members 40 on a surface of a fin 32 used for an evaporator, according to the second embodiment.
[0088]In the second embodiment, as shown in FIG. 8, plural thermal deformation members 40 are arranged in dispersion in the entire range of the surface of the fin 32, to be separated, from each other. Furthermore, a distance L1 between adjacent thermal deformation members 40 at an upstream air side is made larger than a distance L2 between adjacent thermal deformation members 40 at a downstream air side, as shown in FIG. 8.
[0089]In addition, the size of the thermal deformation member 40 located at an upstream air side is made larger than the size of the thermal deformation member 40 located at a downstream air side. The sizes of the thermal deformation members 40 arranged in the air flow direction may be set gradually smaller alon...
third embodiment
[0093]A third embodiment of the present invention will be described with reference to FIGS. 9A and 9B. FIGS. 9A and 9B are schematically sectional views showing thermal deformation members 40 on the surface of the fin 32 used for an evaporator, according to the third embodiment.
[0094]In the present embodiment, the thermal deformation member 40 is made of a bimetal 43. This bimetal 43 is formed by bonding two-kind metal materials 43a, 43b having different thermal expansion coefficients. The thermal deformation members 40 configured by the bimetal 43 are disposed on the surface of the fin 32, such that the metal material 43a with a low thermal expansion coefficient is positioned outside of the bimetal 43, and the metal material 43b with a high thermal expansion coefficient is positioned to contact the surface of the fin 32.
[0095]Thus, in the temperature range where the surface temperature of the fin 32 is lower than material deformation temperature, the bimetal 43 becomes in a flat sh...
PUM
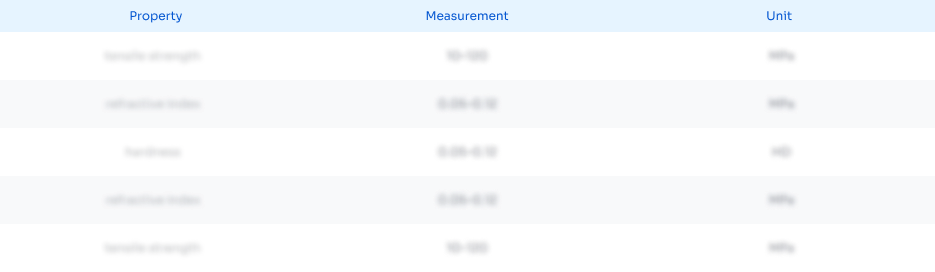
Abstract
Description
Claims
Application Information

- Generate Ideas
- Intellectual Property
- Life Sciences
- Materials
- Tech Scout
- Unparalleled Data Quality
- Higher Quality Content
- 60% Fewer Hallucinations
Browse by: Latest US Patents, China's latest patents, Technical Efficacy Thesaurus, Application Domain, Technology Topic, Popular Technical Reports.
© 2025 PatSnap. All rights reserved.Legal|Privacy policy|Modern Slavery Act Transparency Statement|Sitemap|About US| Contact US: help@patsnap.com