Freefall pyrolytic oven
- Summary
- Abstract
- Description
- Claims
- Application Information
AI Technical Summary
Benefits of technology
Problems solved by technology
Method used
Image
Examples
third embodiment
[0037]Those ordinary skill in the art will also appreciate that the oven 20 is may be modified to manipulate the retention time of material freefalling through the reaction vessel. In a third embodiment, referring to FIGS. 5-8, an oven 20 is similar to the oven shown in FIG. 1 except that the heat transfer plates 60 are mounted adjustably hinged to the reaction vessel 21 rear wall 65 to variably tilt downward depending on the thermal conversion requirments of the particular waste material being charred. The heat transfer plates 60 are once again typically flat, rectangular hollow plates with solid top 75, bottom 76, front side 73, and rear side 77 surfaces, and made from a high heat conductive and resilient material. In this embodiment, the plates 60 include openings 64 positioned typically on the plate end tilted downward and further include a hinge bolt 62 mounted intermediately along the length of the heat transfer plate 62 through bores 69 located on the forward facing wall 73 a...
fourth embodiment
[0041]A skilled artisan will also recognize that the workman may require a convenient means to install and remove plates as necessary to adjust the material fall path. For these instances, in a fourth embodiment, an oven 20 may be designed to slide heat transfer plates 80 in from the exterior through a removable surface 94 of the heating shell 22 and removable reaction vessel rear wall 98 or front reaction vessel wall (not shown) (FIG. 9). This embodiment is similar to the embodiment shown in FIG. 1 except that heat transfer plate 80 may be slid into a mounted position through slots 72 located in the side walls 25. The heat transfer plate 80 is similar to the heat transfer plates 32 and shown in FIG. 1 also incorporating solid top, bottom and side surfaces with a hollow interior and openings 82 on each plate end. The slots 72 incorporate thermal ports 74 that are aligned with thermal intake ports 82 on plates 80. Slot caps 70 are designed to cover slots 72 not supporting a heat tran...
PUM
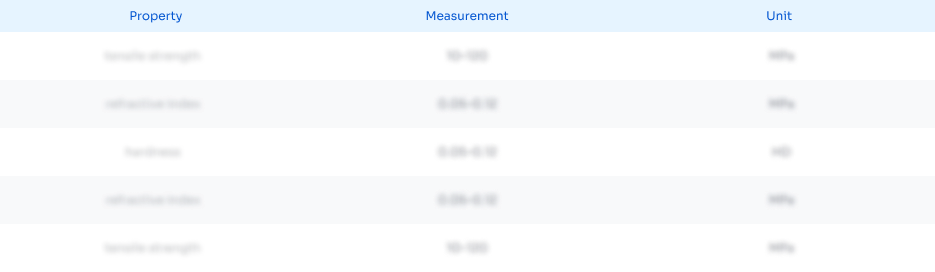
Abstract
Description
Claims
Application Information

- R&D
- Intellectual Property
- Life Sciences
- Materials
- Tech Scout
- Unparalleled Data Quality
- Higher Quality Content
- 60% Fewer Hallucinations
Browse by: Latest US Patents, China's latest patents, Technical Efficacy Thesaurus, Application Domain, Technology Topic, Popular Technical Reports.
© 2025 PatSnap. All rights reserved.Legal|Privacy policy|Modern Slavery Act Transparency Statement|Sitemap|About US| Contact US: help@patsnap.com