Integrated current sensor
- Summary
- Abstract
- Description
- Claims
- Application Information
AI Technical Summary
Benefits of technology
Problems solved by technology
Method used
Image
Examples
Embodiment Construction
[0030] Referring to FIG. 1, a miniaturized, integrated current sensor 10 includes a magnetic field transducer, here in the form of Hall effect sensor 12, a current-carrying conductor 16 and a magnetic core 24. The conductor 16 includes features for receiving portions of the Hall effect sensor 12 and the magnetic core 24 such that the elements are maintained in a fixed position relative to each other. In the illustrated embodiment, the conductor 16 has a first notch 18a and a second notch 18b substantially aligned with the first notch. In assembly, at least a portion of the Hall effect sensor 12 is disposed in the first notch 18a. The magnetic core 24 is substantially C-shaped and has a central region 24a and a pair of substantially parallel legs 24b, 24c extending from the central region. In assembly, at least a portion of the central region 24a is disposed in the second notch 18b of the conductor such that each leg 24b, 24c covers at least a portion of a respective surface of the H...
PUM
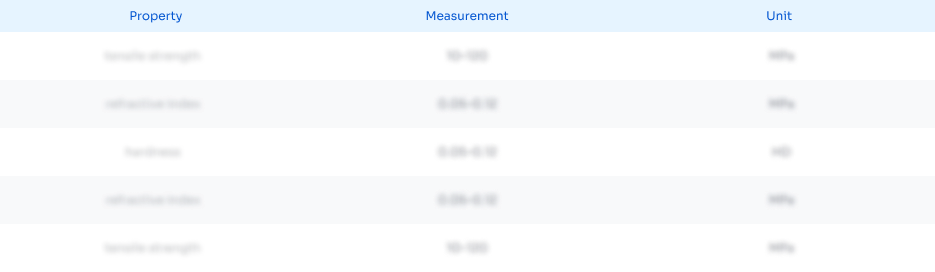
Abstract
Description
Claims
Application Information

- R&D
- Intellectual Property
- Life Sciences
- Materials
- Tech Scout
- Unparalleled Data Quality
- Higher Quality Content
- 60% Fewer Hallucinations
Browse by: Latest US Patents, China's latest patents, Technical Efficacy Thesaurus, Application Domain, Technology Topic, Popular Technical Reports.
© 2025 PatSnap. All rights reserved.Legal|Privacy policy|Modern Slavery Act Transparency Statement|Sitemap|About US| Contact US: help@patsnap.com