Scale-inhibited water reduction in solutions and slurries
a technology of water reduction and solution, applied in the field of scale-inhibited water reduction in solutions and slurries, can solve the problems of difficult finding a permissible site for disposal of such solutions and slurries, difficult to dispose of expensive solutions, and ultimately the problem of disposal or reuse by oil field operators, etc., to enhance improve the efficiency of vaporization, and facilitate reuse.
- Summary
- Abstract
- Description
- Claims
- Application Information
AI Technical Summary
Benefits of technology
Problems solved by technology
Method used
Image
Examples
Embodiment Construction
[0032]FIGS. 1a and 1b show two slightly different variations, and views, of the cavitation devices sometimes known as a cavitation pump, or a cavitation regenerator, and sometimes referred to herein as an SPR, which we use in our invention to regenerate solutions comprising heavy brine components.
[0033]FIGS. 1a and 1b are taken from FIGS. 1 and 2 of Griggs U.S. Pat. No. 5,188,090, which is incorporated herein by reference along with related U.S. Pat. Nos. 5,385,298, 5,957,122, and 6,627,784. As explained in the 5,188,090 patent and elsewhere in the referenced patents, liquid is heated in the device without the use of a heat transfer surface, thus avoiding the usual scaling problems common to boilers and distillation apparatus.
[0034] A housing 10 in FIGS. 1a and 1b encloses cylindrical rotor 11 leaving only a small clearance 12 around its curved surface and clearance 13 at the ends. The rotor 11 is mounted on a shaft 14 turned by motor 15. Cavities 17 are drilled or otherwise cut i...
PUM
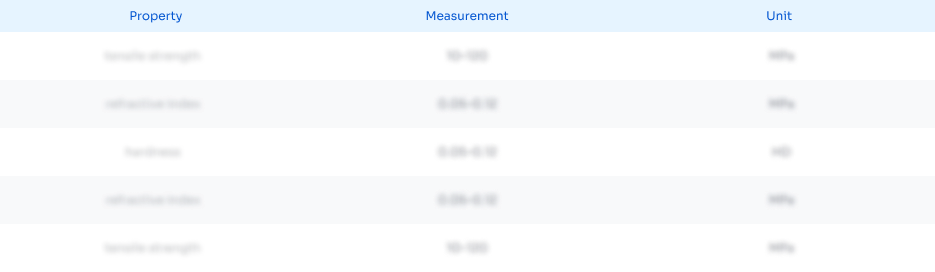
Abstract
Description
Claims
Application Information

- Generate Ideas
- Intellectual Property
- Life Sciences
- Materials
- Tech Scout
- Unparalleled Data Quality
- Higher Quality Content
- 60% Fewer Hallucinations
Browse by: Latest US Patents, China's latest patents, Technical Efficacy Thesaurus, Application Domain, Technology Topic, Popular Technical Reports.
© 2025 PatSnap. All rights reserved.Legal|Privacy policy|Modern Slavery Act Transparency Statement|Sitemap|About US| Contact US: help@patsnap.com