Method and apparatus for fabricating a low density wall panel with interior surface finished
a low density, wall panel technology, applied in the direction of foundation engineering, building components, construction, etc., can solve the problems of high cost, many of the previously used building panels are prone to cracks and other damage, so as to facilitate modification, quickly and efficiently construct modular buildings, and quickly interconnected to exterior service lines
- Summary
- Abstract
- Description
- Claims
- Application Information
AI Technical Summary
Benefits of technology
Problems solved by technology
Method used
Image
Examples
Embodiment Construction
[0049] Referring now to FIGS. 1-13, various embodiments of the present apparatus and method for making the same is provided herein. More specifically, FIG. 1 depicts a construction installation sight identifying an excavation and a foundation wall positioned in place for the placement of a structure such as a single family home. As shown in the photograph, the foundation walls have been installed and secured together similar to a poured foundation, the novelty being that all of the foundation walls have been precast in a manufacturing facility, delivered on location and erected with a crane or other similar means. Furthermore, the foundation and / or wall panels of the present invention utilize a low density foam material positioned between a plurality of ribs made out of concrete, and which may additionally include steel reinforcing bars for structural support. As further shown in these foundation walls, windows or other openings may be provided as necessary. Furthermore, and not sho...
PUM
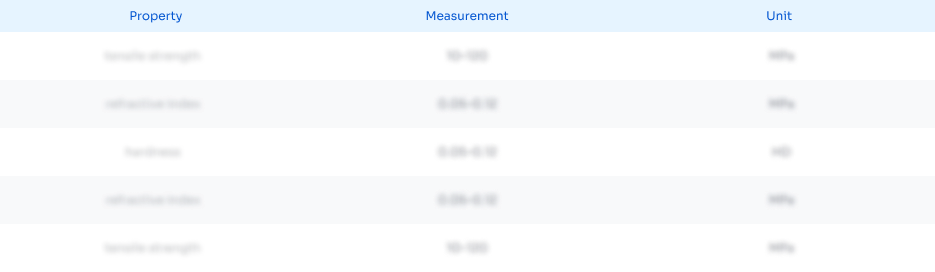
Abstract
Description
Claims
Application Information

- R&D
- Intellectual Property
- Life Sciences
- Materials
- Tech Scout
- Unparalleled Data Quality
- Higher Quality Content
- 60% Fewer Hallucinations
Browse by: Latest US Patents, China's latest patents, Technical Efficacy Thesaurus, Application Domain, Technology Topic, Popular Technical Reports.
© 2025 PatSnap. All rights reserved.Legal|Privacy policy|Modern Slavery Act Transparency Statement|Sitemap|About US| Contact US: help@patsnap.com