Field emission tips, arrays, and devices
a field emission tip and array technology, applied in the field of field emitters, can solve the problems of uniform inability to control the distribution and dimensions inability to achieve uniform distribution of field emission tips, so as to achieve the effect of easy removal and improvement of performan
- Summary
- Abstract
- Description
- Claims
- Application Information
AI Technical Summary
Benefits of technology
Problems solved by technology
Method used
Image
Examples
Embodiment Construction
[0030]FIGS. 1-16 illustrate various methods of forming field emission tips according to the present invention. It should be understood that the illustrations are not meant to be actual views of any particular field emission device, but are merely idealized representations which are employed to more clearly and fully depict the formation of field emission tips of the present invention than would otherwise be possible. Additionally, elements common to FIGS. 1-16 retain the same numerical designation.
[0031]FIGS. 1-4 illustrate one embodiment for forming field emission tips according to the present invention. As shown in FIG. 1, an etch mask material, such as a photoresist material, is patterned by photolithography to define an etch mask element 104 on a substrate 102, such as a wafer of semiconductor material (e.g., silicon) or a silicon on insulator (SOI) type substrate, such as a silicon on glass (SOG) or silicon on sapphire (SOS) substrate. The substrate 102 may also be conductive ...
PUM
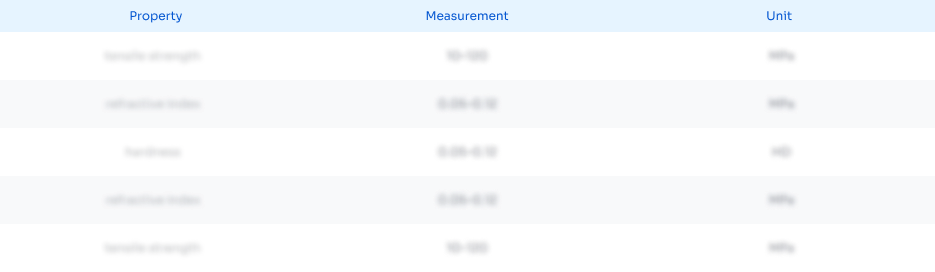
Abstract
Description
Claims
Application Information

- Generate Ideas
- Intellectual Property
- Life Sciences
- Materials
- Tech Scout
- Unparalleled Data Quality
- Higher Quality Content
- 60% Fewer Hallucinations
Browse by: Latest US Patents, China's latest patents, Technical Efficacy Thesaurus, Application Domain, Technology Topic, Popular Technical Reports.
© 2025 PatSnap. All rights reserved.Legal|Privacy policy|Modern Slavery Act Transparency Statement|Sitemap|About US| Contact US: help@patsnap.com