Space vector-based current controlled pwm inverter for motor drives
a technology of space vector and inverter, which is applied in the direction of motor/generator/converter stopper, dynamo-electric converter control, dc motor speed/torque control, etc., can solve the problems of high switching loss, inability to design pmacms with unsurpassed efficiency characteristics, and irregular inverter operation
- Summary
- Abstract
- Description
- Claims
- Application Information
AI Technical Summary
Benefits of technology
Problems solved by technology
Method used
Image
Examples
Embodiment Construction
[0089] Referring to FIG. 19 of the drawings, FIG. 19 is a block diagram of a motor driver according to a preferred embodiment of the present invention in which the motor driver includes a Hall sensor circuit 501, a position detection circuit and current command generation circuit 502, a space vector modulation (SVM) based logic control circuit 503, a pre-drive circuit 504, a current detection resistor 505, and U-phase, V-phase, and W-phase upper side drive transistors 601, 603, and 605, U-phase, V-phase, and W-phase lower side drive transistors 602, 604, and 606, diodes 601D, 602D, 603D, 604D, 605D, and 606D. A motor includes a U-phase coil 701, a V-phase coil 702, and a W-phase coil 703.
[0090] In this embodiment N-type metal oxide semiconductor (NMOS) transistors are used as the drive transistors 601-606. The anode end and cathode end of the diode 601D are connected to the source terminal and drain terminal of the drive transistor 601 respectively. Likewise, the anode end and cath...
PUM
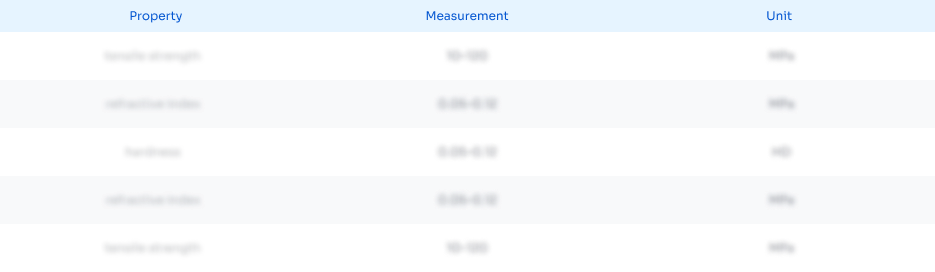
Abstract
Description
Claims
Application Information

- R&D
- Intellectual Property
- Life Sciences
- Materials
- Tech Scout
- Unparalleled Data Quality
- Higher Quality Content
- 60% Fewer Hallucinations
Browse by: Latest US Patents, China's latest patents, Technical Efficacy Thesaurus, Application Domain, Technology Topic, Popular Technical Reports.
© 2025 PatSnap. All rights reserved.Legal|Privacy policy|Modern Slavery Act Transparency Statement|Sitemap|About US| Contact US: help@patsnap.com