Polishing pad and method of polishing a semiconductor wafer
- Summary
- Abstract
- Description
- Claims
- Application Information
AI Technical Summary
Benefits of technology
Problems solved by technology
Method used
Image
Examples
example 1
[0159] The polishing substrate 11 obtained in (2) above was set on a testing bench in such a manner that the surface (polishing surface) having the grooves 13 of the polishing substrate 11 faced down, and the light transmitting member 2 obtained in (1) above was inserted into the through hole. Thereafter, 1 ml of a photocurable adhesive essentially composed of a polyurethane acrylate and an ethylenically unsaturated monomer (Desolite Z8007 having a viscosity at 25.degree. C. of 8,000 mPa.s, manufactured by Japan Fine Coatings Co., Ltd.) was applied to the light transmitting member 2 uniformly, filled in the gap between the outer wall of the light transmitting member 2 and the inner wall of the through hole to ensure that it did not overflow into the polishing surface facing down and cured by exposure to 5,000 J / m.sup.2 of light from a halogen lamp to form an adhesive layer 3, thereby obtaining the polishing pad 1 (I) shown in FIG. 1 and FIG. 20.
[0160] The adhesive used herein had an...
example 2
[0165] The polishing pad (I) obtained in Example 1 was mounted on the platen of a polishing machine equipped with an optical end-point detection device to polish a copper film wafer while slurry containing abrasive particles was supplied at a flow rate of 100 ml / min and a platen revolution of 50 rpm. As a result, the polishing rate was 7,200 .ANG. / min. The slurry did not leak to the non-polishing surface of the polishing pad (I) from the gap between the outer wall of the light transmitting member and the inner wall of the through hole during polishing. No scratch was observed on the polished surface of the copper film wafer when seen through an optical microscope (MX50 of Olympus Co., Ltd.) at a magnification of .times.200 in a dark field mode.
PUM
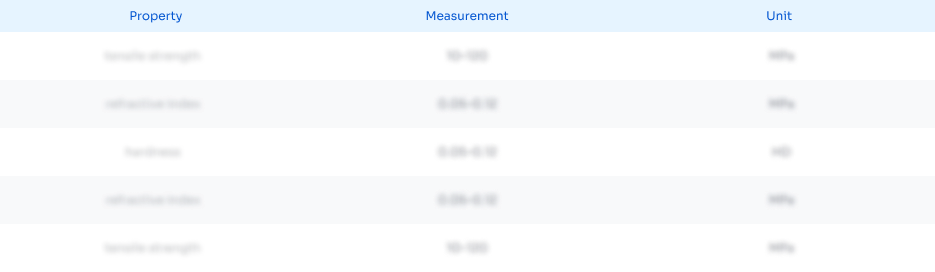
Abstract
Description
Claims
Application Information

- R&D
- Intellectual Property
- Life Sciences
- Materials
- Tech Scout
- Unparalleled Data Quality
- Higher Quality Content
- 60% Fewer Hallucinations
Browse by: Latest US Patents, China's latest patents, Technical Efficacy Thesaurus, Application Domain, Technology Topic, Popular Technical Reports.
© 2025 PatSnap. All rights reserved.Legal|Privacy policy|Modern Slavery Act Transparency Statement|Sitemap|About US| Contact US: help@patsnap.com