Motor and its permanent magnet
- Summary
- Abstract
- Description
- Claims
- Application Information
AI Technical Summary
Benefits of technology
Problems solved by technology
Method used
Image
Examples
Embodiment Construction
[0105] The abovementioned embodiments are one group of examples of practical forms of the present invention, but many other modified examples can be thought of. For example, in the abovementioned embodiment the anisotropic rare earth bonded magnet 13 was magnetized in a 4-pole configuration, but greater than 4 poles is also acceptable. For example, 6poles or8poles are acceptable. If the number of magnetic poles is increased, the magnetic path length gets shorter and therefore the magnetic flux across the armature coils is increased. Moreover, because it is possible to easily magnetize anisotropic rare earth bonded magnet 13, a higher power, quiet motor can be realized.
[0106] Moreover, in the abovementioned embodiment, the anisotropic rare earth bonded magnet 13 is made by resin forming, but it is also acceptable to further process the magnet after resin forming via trimming, etc. for higher precision. With increased dimension precision, a quiet motor without uneven torque is possibl...
PUM
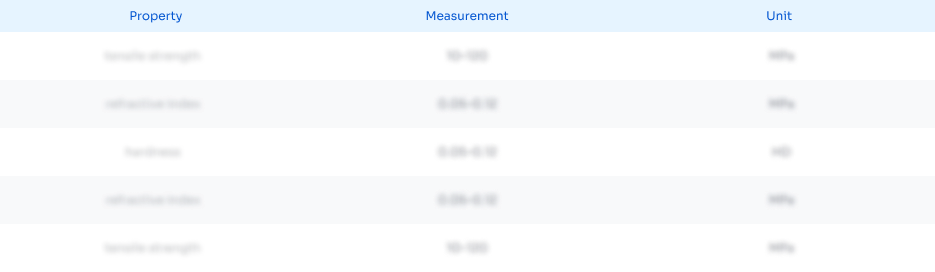
Abstract
Description
Claims
Application Information

- R&D
- Intellectual Property
- Life Sciences
- Materials
- Tech Scout
- Unparalleled Data Quality
- Higher Quality Content
- 60% Fewer Hallucinations
Browse by: Latest US Patents, China's latest patents, Technical Efficacy Thesaurus, Application Domain, Technology Topic, Popular Technical Reports.
© 2025 PatSnap. All rights reserved.Legal|Privacy policy|Modern Slavery Act Transparency Statement|Sitemap|About US| Contact US: help@patsnap.com